Industrial Transmitters: Essential Components for Process Control
Introduction
In modern industrial settings, transmitters play a pivotal role in ensuring efficient and accurate process control. They are responsible for converting physical process variables, such as temperature, pressure, level, and flow, into standardized electrical signals that can be transmitted to control systems, recorders, and other devices. This article delves into the world of industrial transmitters, exploring their types, applications, benefits, and best practices for their effective deployment.
Types of Industrial Transmitters
Industrial transmitters come in various types, each designed to measure and transmit specific process variables. Some of the most common types include:
-
Temperature Transmitters: Measure and transmit the temperature of a process medium (e.g., liquids, gases) using sensors such as thermocouples or resistance temperature detectors (RTDs).
-
Pressure Transmitters: Measure and transmit the pressure of a process fluid (e.g., liquids, gases) using sensors such as diaphragm or Bourdon tubes.
-
Level Transmitters: Measure and transmit the level of a liquid or solid material (e.g., tanks, silos) using sensors such as ultrasonic, capacitance, or float switches.
-
Flow Transmitters: Measure and transmit the flow rate of a fluid (e.g., water, oil, air) using sensors such as vortex shedding, turbine, or magnetic flowmeters.
Applications of Industrial Transmitters
Industrial transmitters find widespread application in various industries, including:



-
Process Industries: Oil and gas production, refining, chemicals, pharmaceuticals
-
Power Generation: Nuclear power plants, thermal power plants, renewable energy systems
-
Water and Wastewater Treatment: Water purification, wastewater treatment, distribution systems
-
Food and Beverage: Processing, packaging, distribution
-
Pharmaceuticals: Manufacturing, storage, distribution
Benefits of Industrial Transmitters
-
Accurate and Reliable Data Transmission: Transmitters convert physical process variables into standardized electrical signals, ensuring accurate and reliable data transmission over long distances without signal degradation.
-
Process Control and Optimization: By providing real-time data on process parameters, transmitters enable precise control and optimization of processes, leading to improved efficiency, safety, and product quality.
-
Remote Monitoring and Alarm Generation: Transmitters can be connected to remote monitoring systems, allowing operators to monitor and respond to process deviations from anywhere in the facility.
-
Integration with Control Systems: Transmitters interface with control systems (e.g., PLCs, DCSs) to provide real-time data for process automation, decision-making, and alarm generation.
-
Compliance with Regulations: Transmitters can help industries comply with safety and environmental regulations by providing accurate data on process parameters and alarm generation for critical conditions.
How Industrial Transmitters Matter
Safety: By providing accurate and reliable process data, transmitters contribute to the safety of industrial processes by detecting hazardous conditions (e.g., high pressure, low flow) and triggering alarms for timely intervention.
Efficiency: Transmitters optimize process control, leading to improved efficiency and reduced energy consumption. Accurate data helps identify areas of waste and optimize processes for maximum performance.
Product Quality: Reliable process data from transmitters enables precise control of process variables, resulting in consistent product quality and reduced waste.



Best Practices for Industrial Transmitters
-
Proper Selection: Carefully select transmitters based on the specific process variable being measured, the required accuracy, and the environmental conditions.
-
Installation: Install transmitters correctly according to the manufacturer's instructions to ensure accurate readings and long-term reliability.
-
Maintenance: Regular maintenance and calibration are essential to maintain accuracy and prevent failures.
-
Calibration: Calibrate transmitters periodically to ensure consistent and reliable readings.
-
Redundancy: Consider redundancy in critical applications by incorporating multiple transmitters to prevent process interruptions in case of failures.
Common Mistakes to Avoid
-
Incorrect Selection: Selecting a transmitter with inadequate accuracy or unsuitable for the process variable can lead to incorrect data and jeopardize process control.
-
Poor Installation: Improper installation, such as incorrect mounting or electrical wiring, can affect transmitter performance and reliability.
-
Neglecting Maintenance: Insufficient maintenance and calibration can result in inaccurate readings, process disturbances, and premature transmitter failures.
-
Ignoring Temperature Effects: Temperature variations can affect transmitter readings; consider selecting transmitters with built-in temperature compensation or installing them in temperature-controlled environments.
-
Ignoring Pressure Effects: Pressure variations can influence transmitter readings, especially for pressure transmitters; ensure proper pressure rating and installation to avoid measurement errors.
Tips and Tricks
-
Transmitters with Digital Outputs: Digital transmitters provide more accurate and reliable signals than analog transmitters, reducing noise and signal fluctuations.
-
Wireless Transmitters: Wireless transmitters offer flexibility and ease of installation in hard-to-reach areas or applications where wired connections are impractical.
-
HART Transmitters: HART (Highway Addressable Remote Transducer) transmitters provide advanced diagnostic and configuration capabilities over a standard 4-20 mA loop.
-
Explosion-Proof Transmitters: For hazardous environments, select explosion-proof transmitters certified for the specific hazardous area classification.
-
Flow Straighteners: Install flow straighteners upstream of flow transmitters to eliminate flow disturbances and ensure accurate flow measurements.
Table 1: Industrial Transmitter Market Size and Growth
Year |
Market Size (USD Billion) |
Growth Rate (%) |
2022 |
7.8 |
4.5 |
2023 (Forecast) |
8.2 |
5.1 |
2024 (Forecast) |
8.7 |
6.0 |
(Source: Market Research Future, 2022)
Table 2: Key Industrial Transmitter Manufacturers
Manufacturer |
Market Share (%) |
Emerson |
20.5 |
Honeywell |
18.9 |
Siemens |
17.2 |
Yokogawa |
14.8 |
ABB |
13.6 |
(Source: Frost & Sullivan, 2021)
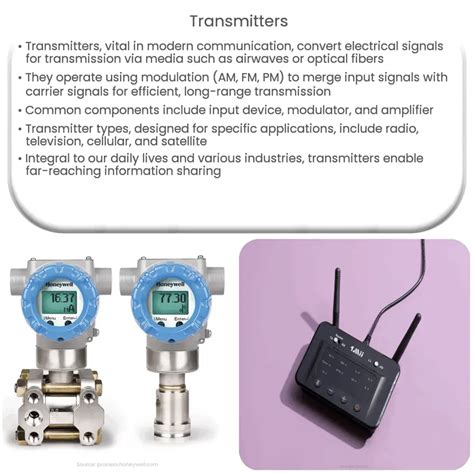
Table 3: Benefits of Industrial Transmitters
Benefit |
Description |
Accurate and Reliable Data Transmission |
Accurate and noise-resistant data transmission over long distances. |
Process Control and Optimization |
Real-time process data for precise control and optimization, improving efficiency and safety. |
Remote Monitoring and Alarm Generation |
Enable remote monitoring and alarm generation for timely intervention and process safety. |
Integration with Control Systems |
Interface with control systems for process automation, decision-making, and alarm generation. |
Compliance with Regulations |
Accurate data for compliance with safety and environmental regulations. |
Conclusion
Industrial transmitters are indispensable components of modern process control systems. They provide accurate and reliable data transmission, enabling precise control, optimization, and safety in various industrial applications. By adhering to best practices and avoiding common mistakes, industries can harness the full potential of industrial transmitters to maximize efficiency, improve product quality, and ensure the safe operation of their processes.