Thrust Bearings: A Comprehensive Guide for Optimal Performance and Reliability
Thrust bearings play a pivotal role in a wide range of industrial and automotive applications, enabling the efficient transfer of axial loads and ensuring smooth operation of rotating machinery. This article provides a comprehensive overview of thrust bearings, covering their types, applications, design considerations, maintenance practices, and troubleshooting techniques. Understanding these aspects is essential for optimizing bearing performance, maximizing equipment lifespan, and minimizing downtime.
Types of Thrust Bearings
Thrust bearings come in various types, each designed to meet specific application requirements. Common types include:
-
Ball Thrust Bearings: Utilize ball elements to accommodate axial loads. They offer high-speed capabilities and low friction, making them suitable for applications such as machine tools, turbines, and pumps.
-
Roller Thrust Bearings: Employ cylindrical or tapered rollers to handle heavy axial loads. They are characterized by high load capacity and durability, making them ideal for heavy-duty applications, including gearboxes, rolling mills, and mining equipment.
-
Needle Thrust Bearings: Feature small, cylindrical rollers known as needles. They offer compact designs and high load capacity in a small axial space, making them useful in space-constrained applications such as vehicle transmissions and aerospace components.
-
Hybrid Thrust Bearings: Combine ball or roller elements with ceramic or other wear-resistant materials. They provide enhanced performance, durability, and corrosion resistance for demanding applications, such as high-temperature environments and corrosive fluids.
-
Hydrodynamic Thrust Bearings: Utilize a fluid film to separate the bearing surfaces. They offer high load capacity and low friction, but require a constant fluid supply and are sensitive to contamination.
Applications of Thrust Bearings
Thrust bearings find application in various industries, including:
-
Power Generation: Turbines, generators, and compressors
-
Automotive: Transmissions, gearboxes, and differentials
-
Industrial Machinery: Pumps, compressors, and rolling mills
-
Aerospace: Engines, landing gear, and flight control systems
-
Mining and Construction: Excavators, cranes, and boring machines
Design Considerations for Thrust Bearings
When selecting and designing thrust bearings, several factors must be considered:
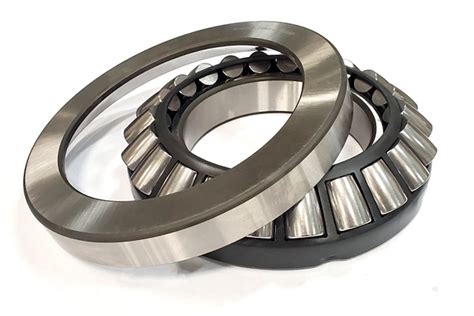
-
Load Capacity: The bearing must be able to withstand the anticipated axial loads while maintaining acceptable safety factors.
-
Speed: The bearing must operate reliably at the required rotational speed.
-
Temperature: The bearing must be suitable for the operating temperature range to prevent premature failure due to overheating or lubrication breakdown.
-
Lubrication: The bearing must be lubricated appropriately to minimize friction and wear.
-
Material: The bearing components must be made of compatible materials to ensure longevity and performance.
-
Mounting: The bearing must be properly mounted and aligned to prevent premature wear or failure.
Maintenance Practices for Thrust Bearings
Proper maintenance is essential for maximizing the lifespan of thrust bearings. Regular inspections, lubrication, and condition monitoring can help detect potential issues early on.

-
Inspections: Visual inspections and vibration analysis can identify potential problems, such as contamination, misalignment, or excessive wear.
-
Lubrication: Maintaining proper lubrication is critical. Lubricant selection, frequency of application, and condition monitoring are important factors.
-
Condition Monitoring: Advanced techniques, such as vibration analysis, temperature monitoring, and oil analysis, can provide valuable insights into bearing health and predict potential failures.
Troubleshooting Thrust Bearing Issues
Common problems encountered with thrust bearings include:

-
Excessive Noise: Can indicate misalignment, lubrication issues, or bearing damage.
-
Vibration: May be caused by misalignment, unbalance, or bearing wear.
-
Overheating: Can result from lubrication problems, excessive loads, or bearing damage.
-
Premature Failure: Can be caused by improper installation, overload, contamination, or lubrication starvation.
Why Thrust Bearings Matter
Thrust bearings are critical components that:
-
Enable Axial Load Transfer: They facilitate the transmission of axial forces in rotating machinery.
-
Reduce Friction and Wear: They minimize friction between moving surfaces, extending equipment lifespan and improving efficiency.
-
Support High Loads: Certain types of thrust bearings can withstand substantial axial loads, making them suitable for heavy-duty applications.
-
Ensure Smooth Operation: They promote smooth rotation by reducing vibration and noise, which is essential for precision machinery.
Benefits of Using Thrust Bearings
-
Improved Performance: Optimized load capacity and reduced friction lead to increased efficiency and reliability.
-
Extended Equipment Lifespan: Proper bearing maintenance can significantly extend the lifespan of rotating machinery.
-
Reduced Downtime: Early detection and correction of bearing issues minimize unplanned downtime, saving time and resources.
-
Energy Savings: Low-friction bearings contribute to energy savings by reducing power consumption in rotating equipment.
Case Stories and Lessons Learned
-
Case Study 1: A power plant experienced premature failure of thrust bearings in its turbine. Investigation revealed improper lubrication, leading to overheating and bearing damage. The plant implemented a rigorous lubrication maintenance program, resulting in a significant reduction in bearing failures and extended turbine lifespan.

-
Lesson Learned: Proper lubrication is crucial for thrust bearing performance and longevity. Regular lubrication and condition monitoring are essential to prevent premature failures.
-
Case Study 2: A manufacturing facility noticed excessive vibration in its gearboxes, which housed thrust bearings. Vibration analysis identified misalignment as the root cause. The facility corrected the alignment, resulting in reduced vibration, improved bearing performance, and reduced noise levels.
-
Lesson Learned: Alignment is critical for thrust bearing performance. Misalignment can lead to premature wear and failure. Regular alignment checks are important to ensure optimal bearing operation.
-
Case Study 3: An aerospace company encountered overheating issues in the thrust bearings of its aircraft engines. Investigation revealed a lack of cooling airflow, leading to elevated bearing temperatures. The company redesigned the cooling system to improve airflow, resulting in reduced bearing temperatures and improved engine performance.
-
Lesson Learned: Bearing cooling is essential to prevent overheating and premature failure. Adequate cooling systems should be designed to maintain proper bearing temperatures.
Common Mistakes to Avoid
-
Overloading: Exceeding the load capacity of thrust bearings can lead to rapid wear and failure.
-
Improper Lubrication: Insufficient or improper lubrication can cause friction, overheating, and premature bearing damage.
-
Misalignment: Incorrect alignment of thrust bearings can lead to premature wear and vibration.
-
Contamination: Contaminants, such as dirt, moisture, or metal particles, can cause bearing damage and premature failure.
-
Improper Mounting: Incorrect mounting or handling of thrust bearings can result in damage or premature failure.
Step-by-Step Approach to Thrust Bearing Maintenance
-
Inspect: Visual inspections and vibration analysis can identify potential issues.
-
Lubricate: Follow the manufacturer's recommendations for lubricant type, quantity, and frequency of application.
-
Monitor: Use condition monitoring techniques, such as vibration analysis and oil analysis, to detect potential problems early on.
-
Troubleshoot: If any issues are detected, consult the manufacturer's guidelines or seek professional assistance to identify and resolve the root cause.
-
Repair or Replace: If necessary, replace or repair the thrust bearing to restore optimal performance and prevent further damage.
Conclusion
Thrust bearings are essential components that play a significant role in the performance and reliability of rotating machinery. Understanding their types, applications, design considerations, maintenance practices, and troubleshooting techniques is crucial for optimizing bearing performance and maximizing equipment lifespan. By following these guidelines and implementing proactive maintenance strategies, organizations can ensure the efficient operation of their machinery, reduce downtime, and achieve enhanced productivity.