Thrust Bearings: The Essential Guide for Reliable Axial Load Management
Thrust bearings are indispensable components in diverse industrial and engineering applications, playing a pivotal role in handling axial loads and ensuring smooth, efficient operation. This comprehensive guide will delve deep into the world of thrust bearings, exploring their types, applications, advantages, drawbacks, and best practices for selection and maintenance.
Types of Thrust Bearings
Thrust bearings come in various designs to suit different load capacities and operating conditions:
-
Ball Thrust Bearings: Utilizes ball elements to support axial loads. They offer high speed capability and moderate load capacity.
-
Roller Thrust Bearings: Employs cylindrical or tapered rollers to handle heavy axial loads. They exhibit higher load capacity but lower speed capability compared to ball bearings.
-
Spherical Roller Thrust Bearings: Combines the advantages of ball and roller bearings, providing exceptional load capacity and self-aligning capabilities under misalignment conditions.
-
Hydrodynamic Thrust Bearings: Operates on the principle of fluid film lubrication, generating a hydrodynamic pressure that supports axial loads and minimizes friction.
-
Magnetic Thrust Bearings: Utilizes magnetic levitation to support axial loads, offering frictionless operation, high speed capability, and reduced maintenance requirements.
Applications of Thrust Bearings
Thrust bearings find widespread applications in industries such as:
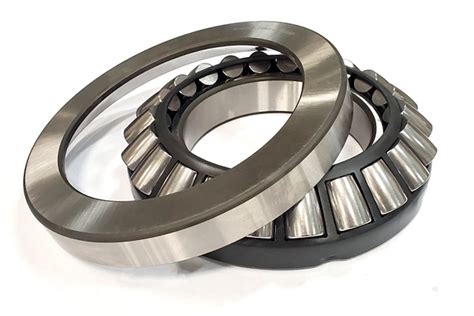
- Power generation: Turbines, generators, and pumps
- Aerospace: Aircraft engines and landing gear
- Automotive: Transmissions and differentials
- Heavy machinery: Cranes, forklifts, and earthmoving equipment
- Steel production: Rolling mills and continuous casters
Advantages of Thrust Bearings
-
Efficient Axial Load Support: Thrust bearings effectively manage axial loads, ensuring smooth operation and preventing damage to mating components.
-
Speed and Accuracy: Bearings with ball or roller elements enable high-speed operation with minimal friction, enhancing efficiency and precision.
-
Durability: Thrust bearings are designed to withstand substantial loads and challenging operating conditions, extending their lifespan.
-
Self-Aligning Capabilities: Spherical roller thrust bearings compensate for misalignment between rotating elements, reducing wear and extending bearing life.
Disadvantages of Thrust Bearings
-
Space Requirements: Thrust bearings require axial space for installation, which may be a limitation in compact designs.
-
Cost: Compared to radial bearings, thrust bearings can be more expensive, especially for high-capacity applications.
-
Maintenance: Thrust bearings require regular inspection and maintenance, including lubrication and cleaning, to ensure optimal performance.
Selection and Maintenance of Thrust Bearings
To maximize performance and longevity, consider the following factors when selecting and maintaining thrust bearings:
-
Load Capacity: Determine the maximum axial load that the bearing must support.
-
Speed: Consider the rotational speed of the bearing in relation to its load capacity and design limitations.
-
Environmental Conditions: Bearings should be compatible with the operating temperature, humidity, and presence of contaminants.
-
Lubrication: Use the appropriate lubrication method based on the bearing type and operating conditions.
-
Inspection and Maintenance: Regularly inspect bearings for wear, damage, or contamination and perform necessary maintenance to ensure optimal operation.
Effective Strategies for Using Thrust Bearings
-
Optimize Load Distribution: Distribute axial loads evenly across the bearing to reduce wear and extend bearing life.
-
Proper Lubrication: Ensure sufficient lubrication to minimize friction and protect bearing components.
-
Regular Monitoring: Regularly monitor bearings for temperature, vibration, and noise levels to detect potential issues early on.
-
Prevent Contamination: Protect bearings from contaminants such as dirt, moisture, and abrasive particles that can cause premature wear.
-
Avoid Misalignment: Ensure proper alignment between rotating elements to prevent uneven loading and reduce bearing stress.
Common Mistakes to Avoid
-
Overloading: Operating bearings beyond their rated load capacity can lead to premature failure and damage.
-
Improper Lubrication: Insufficient or incorrect lubrication can result in friction, wear, and overheating.
-
Neglecting Maintenance: Ignoring regular inspection and maintenance can compromise bearing performance and shorten its lifespan.
-
Contamination: Allowing contaminants to enter the bearing can cause abrasive wear and reduce bearing life.
-
Misalignment: Improper alignment between rotating elements can lead to uneven loading and premature bearing failure.
Step-by-Step Approach for Thrust Bearing Installation
-
Prepare the Bearing Seat: Ensure the bearing seat is clean, smooth, and free of burrs or defects.
-
Install the Thrust Washer: Place the thrust washer on the seating surface, ensuring it is properly aligned.
-
Lubricate the Bearing: Apply the specified lubricant to the bearing surfaces before installation.
-
Mount the Bearing: Carefully position and mount the bearing on the thrust washer.
-
Tighten the Bearing: Secure the bearing using nuts or bolts, ensuring proper torque as per manufacturer specifications.
-
Verify Alignment: Verify proper alignment between the rotating elements and adjust as necessary.
-
Test the Bearing: Conduct a test run to ensure smooth operation and monitor temperature, vibration, and noise levels.
Key Performance Indicators for Thrust Bearings
-
Axial Load Capacity: Maximum axial load that the bearing can withstand without failure.
-
Speed Limit: Maximum rotational speed that the bearing can operate reliably.
-
Operating Temperature Range: Temperature range within which the bearing can operate efficiently.
-
Lubrication Interval: Time interval between lubrication cycles to maintain optimal bearing performance.
-
Mean Time Between Failures (MTBF): Estimated time interval between bearing failures.
Conclusion
Thrust bearings play a critical role in supporting axial loads and ensuring smooth operation of rotating machinery. By understanding their types, applications, advantages, and drawbacks, engineers and technicians can optimize thrust bearing selection and maintenance practices to maximize equipment performance, reduce downtime, and enhance safety. Adhering to effective strategies, avoiding common mistakes, and following a step-by-step approach for installation and maintenance will ensure the longevity and reliability of thrust bearings in demanding industrial applications.
Tables
Table 1: Thrust Bearing Types and Characteristics
Type |
Elements |
Load Capacity |
Speed Capability |
Self-Alignment |
Ball Thrust Bearing |
Balls |
Moderate |
High |
No |
Roller Thrust Bearing |
Cylindrical or tapered rollers |
High |
Moderate |
No |
Spherical Roller Thrust Bearing |
Spherical rollers |
Exceptional |
Moderate |
Yes |
Hydrodynamic Thrust Bearing |
Fluid film |
Low to moderate |
High |
Yes |
Magnetic Thrust Bearing |
Magnetic levitation |
Low to moderate |
High |
Yes |
Table 2: Thrust Bearing Applications in Different Industries
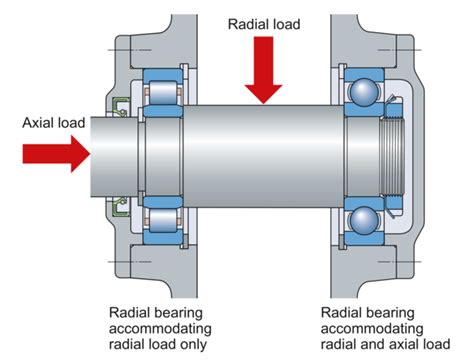
Industry |
Applications |
Power Generation |
Turbines, generators, pumps |
Aerospace |
Aircraft engines, landing gear |
Automotive |
Transmissions, differentials |
Heavy Machinery |
Cranes, forklifts, earthmoving equipment |
Steel Production |
Rolling mills, continuous casters |
Table 3: Common Thrust Bearing Problems and Causes
Problem |
Cause |
Wear or damage |
Overloading, improper lubrication, contamination |
Excessive noise or vibration |
Misalignment, worn bearings |
Overheating |
Insufficient lubrication, bearing seal failure |
Premature failure |
Contamination, improper installation, misalignment |
Reduced efficiency |
Bearing degradation, lubrication issues |