A Comprehensive Installation Manual for Tumbler Screeners: A Step-by-Step Guide to Efficient Operation
Introduction
Tumbler screeners, essential equipment in various industries, are used to separate materials based on size and shape. Proper installation is crucial to ensure optimal performance and longevity of the equipment. This comprehensive manual provides a step-by-step guide to installing tumbler screeners, addressing every crucial step to ensure a successful installation process.
1. Pre-Installation Preparations
-
Select a Suitable Location: Choose a level, stable surface that can withstand the weight of the screener and accommodate its operating dimensions.
-
Prepare the Foundation: Create a solid foundation that meets the manufacturer's specifications for load-bearing capacity. A concrete slab is often recommended.
-
Gather Necessary Tools and Materials: Ensure you have all the necessary tools, including a level, wrenches, torque wrench, and any additional materials specified by the manufacturer.
2. Unpacking and Assembling the Screener

-
Unpack the Screener Carefully: Open the packaging with care and inspect the equipment for any damage.
-
Identify the Components: Lay out all the components and identify them according to the manufacturer's instructions.
-
Assemble the Screener: Follow the manufacturer's instructions to assemble the screener, including mounting the screen meshes and attaching the drive motor.
3. Leveling and Alignment
-
Level the Screener: Use a level to ensure that the screener is perfectly level in all directions.
-
Align the Motor: Align the drive motor correctly according to the manufacturer's instructions to prevent misalignment and premature wear.
-
Check Belt Tension: Ensure that the drive belt is properly tensioned to prevent slippage and excessive wear.
4. Connecting Utilities
-
Electrical Connection: Connect the screener to an appropriate power source, following the manufacturer's electrical specifications.
-
Inlet and Outlet Connections: Attach the inlet and outlet chutes to the screener, ensuring a proper fit to prevent material spillage.
-
Safety Measures: Implement necessary safety measures, including guarding the rotating parts and providing emergency stop buttons.
5. Test Run and Adjustments
-
Initial Test Run: Start the screener and observe its operation. Check for abnormal sounds or vibrations.
-
Adjustments: Make any necessary adjustments, such as fine-tuning the screen mesh angle or adjusting the belt tension, to optimize performance.
-
Verification: Verify that the screener is operating efficiently and producing the desired separation results.
Why Installation Matters
Proper installation of tumbler screeners is essential for several reasons:
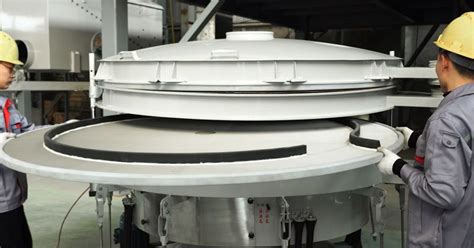
-
Optimal Performance: A well-installed screener runs smoothly, minimizes downtime, and achieves optimal separation efficiency.
-
Longevity: Correct installation extends the lifespan of the screener by preventing misalignment, premature wear, and potential failures.
-
Safety: Proper installation ensures that the screener operates safely, reducing the risk of accidents and injuries.
Benefits of a Properly Installed Screener
-
Increased Productivity: Optimized performance leads to higher throughput and increased production capacity.
-
Reduced Maintenance Costs: Proper installation minimizes wear and tear, reducing the frequency and cost of maintenance.
-
Improved Product Quality: Accurate separation ensures consistent product quality and reduces the need for reprocessing.
-
Enhanced Safety: Safe operation protects employees and the work environment.
Pros and Cons of Tumbler Screeners
Pros:
-
Versatility: Separates a wide range of materials, including aggregates, minerals, food products, and waste.
-
Efficiency: Delivers high-quality separation even with complex materials.
-
Durability: Robust construction ensures reliable operation for extended periods.
Cons:
-
Power Consumption: High-power motors may require significant energy consumption.
-
Noise Generation: Screening operations can generate noise, especially when handling larger materials.
-
Limited Capacity: May be unsuitable for large-scale, high-volume separation applications.
Tips and Tricks
-
Monitor the drive motor: Observe the motor temperature and current draw to detect any abnormalities.
-
Clean the screen meshes regularly: Remove debris or blinding material from the screen meshes to maintain optimal separation efficiency.
-
Implement dust control measures: Suppress dust generation to improve the work environment and prevent contamination.
Stories and Lessons Learned

Story 1: A cement plant experienced premature bearing failure in their tumbler screener. Investigation revealed that the screener was not properly leveled, causing excessive vibration and stress on the bearings.
Lesson: Proper leveling is crucial to prevent misalignment and premature wear.
Story 2: A mining operation had difficulties achieving the desired separation efficiency with their tumbler screener. Adjustments to the screen mesh angle and feed rate were ineffective.
Lesson: Sometimes, the root cause of separation issues lies in the screening process itself, and adjustments to the equipment may not be enough.
Story 3: A waste recycling facility upgraded to a tumbler screener with a higher capacity. However, the increased throughput resulted in significant dust generation.
Lesson: Consider the capacity and potential impact on the work environment when selecting a tumbler screener.
Tables
Table 1: Recommended Foundation Specifications for Tumbler Screeners
Screener Size (ft²) |
Concrete Thickness (in) |
Minimum Compressive Strength (psi) |
50-100 |
6 |
3,000 |
100-200 |
8 |
3,500 |
200-400 |
10 |
4,000 |
Table 2: Safety Precautions for Tumbler Screener Operation
- Wear appropriate personal protective equipment (PPE).
- Keep loose clothing and jewelry away from moving parts.
- Ensure proper guarding of all rotating components.
- Provide emergency stop buttons and warning labels.
- Regularly inspect and maintain the screener.
Table 3: Troubleshooting Common Tumbler Screener Issues
Issue |
Possible Cause |
Solution |
Poor separation |
Incorrect screen mesh size, angle, or feed rate |
Adjust parameters or consult with a screening expert |
Excessive vibration |
Misalignment, loose bearings, uneven material distribution |
Level the screener, tighten bearings, rebalance material feed |
Drive motor overheating |
Overload, misalignment, belt slippage |
Reduce feed rate, check alignment, tension belt |