Bearings: The Key Components for Smooth and Efficient Motion
Bearings are crucial components in various industrial and domestic applications, enabling smooth rotation and reducing friction between moving parts. They play a vital role in the performance and longevity of machinery, vehicles, and everyday devices. Understanding the different types of bearings, their applications, and maintenance practices is essential for maximizing their effectiveness and extending their lifespan.
Types of Bearings
The diverse range of bearing types available caters to specific requirements and operating conditions. Each type offers unique advantages and considerations:
1. Rolling Element Bearings

-
Ball Bearings: Utilize spherical balls as rolling elements, offering low friction and high load capacity. Ideal for moderate speeds and radial loads.
-
Roller Bearings: Employ cylindrical or tapered rollers, providing higher load-carrying capacity and can withstand axial loads. Suitable for heavy machinery and high-speed applications.
-
Needle Bearings: Incorporate thin, cylindrical rollers, allowing for compact designs with low friction and high load capacity. Often used in limited radial space scenarios.
2. Plain Bearings
-
Journal Bearings: Consist of a rotating shaft supported by a stationary bearing surface. Suitable for low-speed, high-load applications where lubrication is critical.
-
Thrust Bearings: Similar to journal bearings but designed to support axial loads. Used in pumps, compressors, and other applications where thrust forces are present.
-
Hydrodynamic Bearings: Utilize a thin layer of fluid between the bearing surfaces to create hydrodynamic lift, reducing friction and allowing for high speeds.
3. Other Bearing Types
-
Magnetic Bearings: Employ magnetic forces to levitate the rotating element, eliminating friction and providing vibration-free operation. Used in high-performance applications such as aerospace and medical devices.
-
Air Bearings: Utilize a thin layer of compressed air between the bearing surfaces to reduce friction and provide high precision. Ideal for applications requiring contamination-free environments.
Applications of Bearings
Bearings find applications across a wide spectrum of industries, including:
-
Industrial Machinery: Used in conveyors, pumps, compressors, and other heavy-duty machinery to reduce friction and improve efficiency.
-
Automotive Industry: Essential in engines, transmissions, and wheel assemblies to facilitate smooth rotation and enhance performance.
-
Aerospace: Bearings play a critical role in aircraft engines, turbines, and landing gear, ensuring safety and reliability.
-
Household Appliances: Found in refrigerators, washing machines, and other appliances to minimize friction and extend lifespan.
-
Medical Devices: Bearings are utilized in surgical instruments, prosthetics, and imaging equipment, ensuring precise and reliable operation.
Bearing Maintenance and Reliability
Regular maintenance practices are essential to ensure optimal bearing performance and longevity:
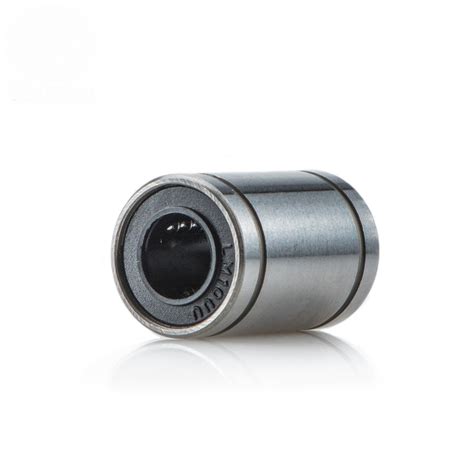
1. Lubrication: Proper lubrication is crucial to minimize friction and wear. The frequency and type of lubrication depend on the bearing type and operating conditions.
2. Inspection: Regular inspections can identify potential problems, such as wear, contamination, or improper alignment, allowing for timely corrective actions.
3. Monitoring: Condition monitoring techniques, such as vibration analysis and temperature monitoring, can provide insights into bearing health and predict potential failures.
4. Replacement: Worn or damaged bearings should be promptly replaced to avoid further damage and ensure continued reliability.
Tips and Tricks for Enhanced Bearing Performance
-
Correct Bearing Selection: Choosing the appropriate bearing for the specific application is crucial. Factors to consider include load capacity, speed, lubrication, and environmental conditions.
-
Proper Installation: Incorrect installation can lead to premature bearing failure. Ensure precise alignment and adequate lubrication during installation.
-
Avoid Overloading: Exceeding the bearing's load capacity can cause rapid wear and potential damage.
-
Lubrication Best Practices: Use the correct lubricant type and quantity recommended for the specific bearing and application.
-
Regular Cleaning: Contaminants, such as dirt and moisture, can accelerate bearing wear. Regular cleaning helps maintain optimal performance.
Common Mistakes to Avoid
-
Ignoring Lubrication: Insufficient or improper lubrication can lead to premature bearing failure.
-
Overtightening Bearings: Excessive tightening can put unnecessary stress on the bearing and cause overheating or damage.
-
Ignoring Inspection and Monitoring: Regular inspections and condition monitoring are crucial for identifying potential problems and avoiding catastrophic failures.
-
Using Incorrect Bearing Type: Selecting the wrong bearing for the application can result in reduced performance and premature failure.
-
Poor Installation Practices: Incorrect alignment or inadequate lubrication during installation can lead to early bearing damage.
Step-by-Step Approach to Bearing Maintenance
-
Monitor Bearing Operation: Regularly assess bearing performance through visual inspection, vibration analysis, or other condition monitoring techniques.
-
Identify Potential Issues: Note any unusual noises, vibrations, or excessive heat, which may indicate potential problems.
-
Lubricate Regularly: Follow the recommended lubrication schedule and use the correct lubricant type and quantity.
-
Inspect Regularly: Perform periodic visual inspections to check for wear, contamination, or misalignment.
-
Clean Bearings: Regularly clean bearings to remove contaminants and prevent premature failure.
-
Replace Worn or Damaged Bearings: Promptly replace bearings that show signs of significant wear or damage to avoid further issues.
Pros and Cons of Different Bearing Types
Pros and Cons of Rolling Element Bearings
-
Rolling Element Bearings
-
Pros: Low friction, high load capacity, suitable for high speeds.
-
Cons: Requires lubrication, can generate noise, may require complex mounting.
Pros and Cons of Plain Bearings
-
Plain Bearings
-
Pros: Simple design, low cost, suitable for low speeds and high loads.
-
Cons: Requires constant lubrication, can be susceptible to wear and contamination.
Pros and Cons of Other Bearing Types
-
Magnetic Bearings
-
Pros: Vibration-free, high speed, low maintenance.
-
Cons: Expensive, requires specialized knowledge for installation and maintenance.
-
Air Bearings
-
Pros: High precision, contamination-free, no lubrication required.
-
Cons: Sensitive to environmental conditions, can be noisy.
Key Performance Indicators for Bearing Reliability
-
Mean Time Between Failures (MTBF): Average time between bearing failures, indicating overall bearing reliability.
-
Bearing Life: Expected lifespan of a bearing under specific operating conditions.
-
Failure Rate: Rate at which bearings fail, commonly expressed as failures per million operating hours.
-
Reliability and Availability: Consistency and frequency of bearing operation, affecting machine uptime and productivity.
Tables for Bearing Considerations
Table 1: Bearing Type Characteristics
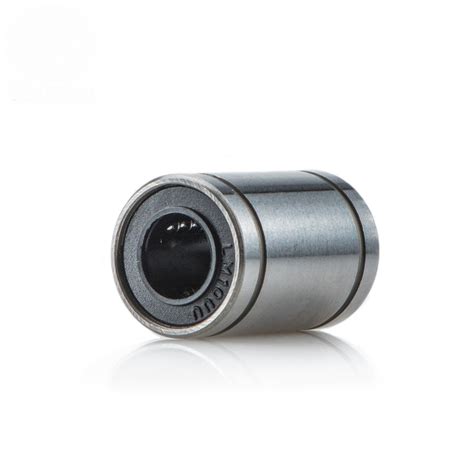
Bearing Type |
Rolling Element |
Friction |
Load Capacity |
Speed |
Ball Bearing |
Spherical balls |
Low |
Moderate |
Moderate |
Roller Bearing |
Cylindrical/tapered rollers |
Higher |
Higher |
Higher |
Needle Bearing |
Thin, cylindrical rollers |
Very low |
High |
Moderate |
Journal Bearing |
Rotating shaft supported by stationary surface |
Medium |
Low |
Low |
Thrust Bearing |
Rotating shaft supported axially |
Medium |
Low |
Low |
Table 2: Bearing Applications and Industries
Industry |
Application |
Bearing Type |
Automotive |
Engines, transmissions, wheel assemblies |
Rolling element bearings |
Industrial |
Conveyors, pumps, compressors |
Rolling element bearings, plain bearings |
Aerospace |
Aircraft engines, turbines, landing gear |
Rolling element bearings, magnetic bearings |
Household Appliances |
Refrigerators, washing machines |
Rolling element bearings, plain bearings |
Medical Devices |
Surgical instruments, prosthetics, imaging equipment |
Rolling element bearings, magnetic bearings |
Table 3: Bearing Maintenance Best Practices
Maintenance Practice |
Frequency |
Purpose |
Lubrication |
As per manufacturer's recommendations |
Reduce friction, minimize wear |
Inspection |
Regular intervals |
Identify potential issues, such as wear or contamination |
Monitoring |
Continuous or periodic |
Assess bearing performance and predict potential failures |
Replacement |
As needed |
Ensure optimal performance, prevent failures |