Comprehensive Guide to Thrust Bearings: Maximizing Bearing Performance for Axial Loads
Thrust bearings play a vital role in various mechanical applications by accommodating axial forces, ensuring smooth operation, and extending the life of rotating machinery. This comprehensive guide explores the design, types, materials, applications, maintenance, and troubleshooting techniques of thrust bearings.
1. Understanding Thrust Bearings
Thrust bearings are specifically engineered to withstand and support axial loads, which act parallel to the shaft axis. Unlike radial bearings that manage perpendicular forces, thrust bearings enable rotation while preventing axial displacements.
2. Types of Thrust Bearings
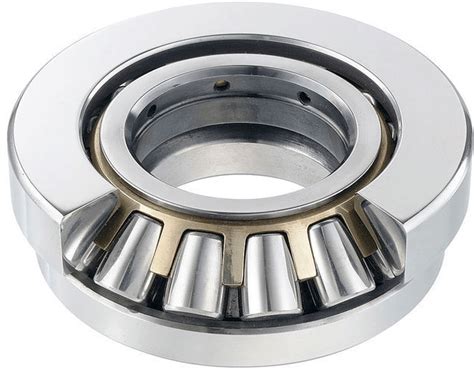
-
Plain Thrust Bearings: Slide on a flat surface, providing low friction and high load capacity.
-
Ball Thrust Bearings: Utilize ball elements to reduce friction and accommodate misalignments.
-
Roller Thrust Bearings: Employ cylindrical or tapered rollers for higher load-carrying capabilities.
-
Hydrostatic Thrust Bearings: Create a thin film of lubricant to support high loads and prevent metal-to-metal contact.
-
Magnetic Thrust Bearings: Utilize electromagnetic forces to levitate the shaft, eliminating friction and wear.
3. Material Considerations
The choice of bearing material depends on several factors, including load capacity, friction, wear resistance, and operating environment.
-
Steel: Commonly used for high load applications, offering high hardness and tensile strength.
-
Bronze: Exhibits good wear resistance and anti-galling properties, suitable for moderate loads.
-
Polymer: Provides low friction and corrosion resistance, ideal for low-load applications.
-
Ceramic: Offers extreme hardness, wear resistance, and high-temperature tolerance.
4. Applications
Thrust bearings find applications in a wide range of industries due to their ability to support axial loads:
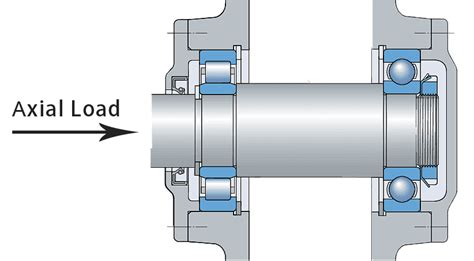
- Automotive: Transmissions, gearboxes, and differentials
- Aerospace: Jet engines, propellers, and flight control systems
- Industrial Machinery: Pumps, compressors, turbines, and motors
- Medical Equipment: Surgical equipment, imaging systems, and prosthetics
5. Maintenance and Troubleshooting
To ensure optimal performance and longevity, proper maintenance is essential:
-
Lubrication: Use appropriate lubricant for the specific bearing type and application.
-
Alignment: Incorrect alignment can lead to premature failure. Verify and adjust alignment regularly.
-
Temperature Monitoring: Excessive heat can damage bearings. Monitor bearing temperature and adjust operating conditions accordingly.
Common Troubleshooting Scenarios:
-
Excessive Noise: May indicate improper lubrication, misalignment, or wear.
-
Shaft Wobble: Can result from incorrect mounting, bearing damage, or shaft misalignment.
-
Failure Under Load: Points to bearing failure due to excessive loading, fatigue, or contamination.
6. Inspirational Stories
-
Case Study: Increased Aircraft Engine Efficiency - By optimizing thrust bearing design, a team of engineers reduced engine friction by 20%, resulting in significant fuel savings and reduced emissions.
-
Patient Success: Enhanced Hip Joint Mobility - A new type of magnetic thrust bearing was developed for hip prosthetics, providing patients with greater range of motion and pain reduction.
-
Innovation: Precision Measurement in Quantum Computers - Thrust bearings are used in quantum computers to minimize vibrational disturbances, enabling precise measurements and improving computing accuracy.
7. Tips and Tricks
- Choose the right bearing type for the specific load and operating conditions.
- Use high-quality lubricants and follow recommended maintenance intervals.
- Monitor bearing performance through regular inspections and data analysis.
- Consider using advanced bearing technologies such as hydrostatic or magnetic bearings for improved efficiency and extended lifetime.
8. Step-by-Step Approach
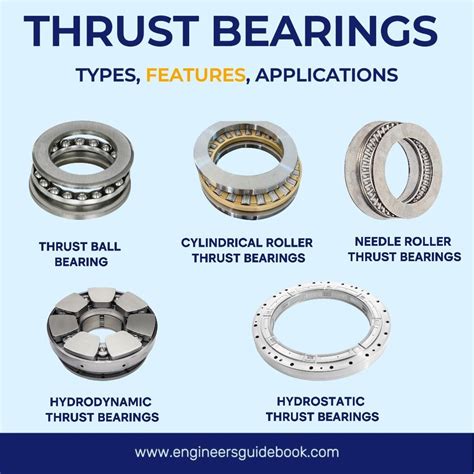
Replacing a Thrust Bearing:
-
Disassemble Assembly: Remove the shaft, housing, and old bearing.
-
Clean Components: Thoroughly clean all components to ensure no debris or contaminants remain.
-
Lubricate Bearing: Apply appropriate lubricant to the new bearing and surrounding components.
-
Install Thrust Bearing: Align and insert the new bearing.
-
Reassemble Assembly: Reinstall the housing, shaft, and any necessary components.
-
Alignment Check: Verify proper alignment using a dial indicator or other precision instrument.
9. FAQs
-
What is the difference between radial and thrust bearings? Radial bearings support loads perpendicular to the shaft axis, while thrust bearings support axial loads.
-
Which type of thrust bearing is suitable for high load applications? Roller thrust bearings are ideal for high load-carrying capacities.
-
How can I prevent thrust bearing failure? Proper lubrication, correct alignment, and temperature monitoring are crucial for longevity.
-
What is the advantage of magnetic thrust bearings? Magnetic thrust bearings eliminate friction, reducing wear and heat generation.
-
How often should I replace thrust bearings? Replacement intervals vary depending on application and usage. Regular inspections and vibration analysis can help determine the optimal replacement schedule.
-
What are the signs of a failing thrust bearing? Excessive noise, shaft wobble, or failure under load may indicate a need for replacement.
Conclusion
Thrust bearings are essential components in various mechanical systems, ensuring smooth operation under axial loads. By understanding their design, types, materials, and maintenance practices, you can optimize bearing performance, extend equipment life, and achieve greater efficiency in your applications.