The Ultimate Guide to Thrust Bearings: Functions, Applications, and Maintenance
Introduction
Thrust bearings are specialized bearings designed to withstand loads applied axially, parallel to the shaft's axis. They play a crucial role in various mechanical systems, including wind turbines, pumps, and machine tools. This comprehensive guide delves into the functions, applications, types, maintenance, and troubleshooting of thrust bearings, providing valuable insights for engineers, technicians, and professionals alike.
Functions of Thrust Bearings
The primary function of a thrust bearing is to support axial loads and prevent relative motion between two surfaces. They operate smoothly under constant or intermittent axial loads, reducing friction and wear. Thrust bearings enable efficient operation of machinery, ensuring longevity and reliability.
Applications of Thrust Bearings
Thrust bearings find application in a wide range of industries, including:
-
Wind turbines: Supporting the weight of the rotor and blades
-
Pumps: Transmitting force from the shaft to the impeller
-
Machine tools: Supporting and guiding the workpiece under axial loads
-
Automotive: Providing axial support in transmissions and differentials
-
Industrial machinery: Supporting rotating shafts in motors, turbines, and compressors
Types of Thrust Bearings
There are various types of thrust bearings designed for specific applications and load requirements. The most common types include:
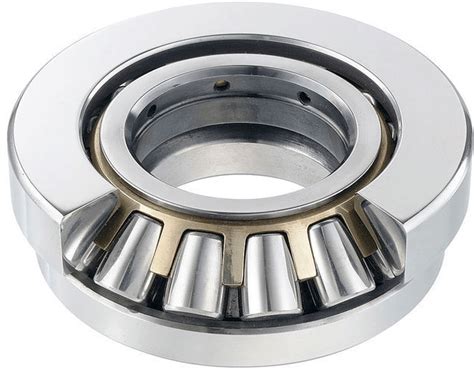
-
Flat contact bearings: Consisting of hardened and ground flat washers that slide against each other, providing low friction and high load capacity
-
Tapered roller bearings: Utilizing rollers that are tapered towards the ends, allowing for higher load ratings than flat contact bearings
-
Spherical roller thrust bearings: Featuring self-aligning spherical rollers, accommodating misalignment and providing high load capacity
-
Gas foil bearings: Utilizing a thin layer of gas to provide frictionless support, ideal for high-speed and high-temperature applications
Maintenance of Thrust Bearings
Proper maintenance is essential to ensure optimal performance and extend the lifespan of thrust bearings. Regular maintenance practices include:
-
Inspection: Visual inspection of the bearing surfaces, races, and cages for wear, damage, or contamination
-
Lubrication: Regular lubrication based on the manufacturer's recommendations to reduce friction and prevent wear
-
Alignment: Checking and adjusting the alignment of the bearing with the shaft and housing
-
Cleaning: Removal of dirt, debris, and contaminants using appropriate cleaning methods
Troubleshooting Thrust Bearings
Identifying and resolving issues with thrust bearings is crucial for maintaining system efficiency and preventing downtime. Common troubleshooting techniques include:

-
Noise analysis: Listening for unusual noises, such as squealing or grinding, that may indicate bearing failure
-
Vibration analysis: Monitoring vibration levels to detect any anomalies that may be caused by misalignment or bearing damage
-
Temperature monitoring: Measuring the bearing temperature to identify overheating, which may indicate excessive friction or lubrication failure
Importance and Benefits of Thrust Bearings
Thrust bearings play a vital role in various industrial and automotive applications by:

-
Reducing friction and wear: Enabling smooth operation of rotating components, minimizing energy loss and extending component lifespan
-
Supporting axial loads: Withstanding axial forces, preventing damage to shafts and other components
-
Improving efficiency: Minimizing energy consumption and maximizing system performance through reduced friction and optimized load distribution
-
Extending equipment lifespan: Proper maintenance and lubrication of thrust bearings contribute to the overall longevity and reliability of machinery
Stories and Lessons
Three compelling stories illustrate the importance of thrust bearings in real-world applications:
-
Wind Turbine Failure Prevention: In a wind turbine, a faulty thrust bearing led to excessive wear and vibration, potentially causing catastrophic damage to the turbine. Timely diagnosis and replacement of the bearing prevented the failure and ensured continued operation.
-
Pump Performance Improvement: In a high-pressure pump, an upgrade to tapered roller thrust bearings resulted in a significant reduction in energy consumption and noise levels. The improved bearing reduced friction and optimized load distribution, leading to enhanced pump efficiency.
-
Machine Tool Reliability Enhancement: A machine tool manufacturer experienced repeated failures of flat contact thrust bearings in its high-speed spindle. By switching to spherical roller thrust bearings, the company significantly increased bearing lifespan and reduced maintenance downtime, improving productivity and reliability.
These stories highlight the critical role thrust bearings play in ensuring the performance, reliability, and safety of industrial machines.

Tips and Tricks
Here are some practical tips and tricks for working with thrust bearings:
- Use high-quality lubricants specifically designed for thrust bearings.
- Avoid overlubrication, as excess grease can attract contaminants and lead to premature bearing failure.
- Regularly monitor bearing clearances and adjust as necessary to prevent excessive play or binding.
- Store thrust bearings in a clean and dry environment to prevent corrosion.
- Consider using thrust bearing retainers to prevent the bearing from disassembling during handling or installation.
Step-by-Step Approach to Thrust Bearing Maintenance
Follow these steps for effective thrust bearing maintenance:
-
Inspection: Remove the bearing and visually inspect for any signs of wear, damage, or contamination.
-
Cleaning: Clean the bearing thoroughly using an appropriate solvent and cleaning method.
-
Lubrication: Apply a thin layer of lubricant to the bearing surfaces according to the manufacturer's specifications.
-
Assembly: Carefully assemble the bearing, ensuring correct orientation and alignment.
-
Testing: Run the bearing under load to check for smooth operation and any unusual noises or vibrations.
Conclusion
Thrust bearings are indispensable components in machinery and equipment that rely on axial load support. Understanding their functions, applications, types, maintenance, and troubleshooting is essential for optimizing performance, ensuring reliability, and preventing costly failures. By implementing the tips and tricks outlined in this guide, professionals can extend the lifespan of thrust bearings, reduce downtime, and maximize the efficiency of their systems.