Thrust Bearings: A Comprehensive Guide to Their Design, Applications, and Maintenance
Introduction
Thrust bearings are a fundamental component in various mechanical systems, enabling the transmission of axial loads while accommodating rotational or oscillatory motion. Due to their crucial role in power transmission and machinery operation, it is essential to understand their design, applications, and maintenance practices.
Understanding Thrust Bearings
Design and Function
Thrust bearings consist of two primary components: a thrust washer and a thrust collar. The thrust washer, typically made of hardened steel or bearing material, provides the load-bearing surface for the axial load. The thrust collar, often manufactured from softer materials such as bronze or cast iron, assists in distributing the load and reducing friction.
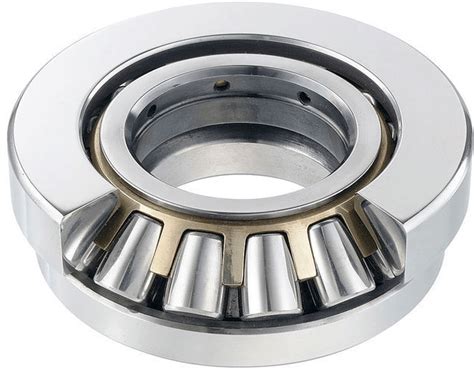
Mechanism of Operation:
Thrust bearings operate by allowing axial motion while constraining radial displacement. As axial load is applied, the thrust washer slides against the thrust collar, minimizing friction and wear.
Types of Thrust Bearings
Based on their design and application requirements, thrust bearings can be classified into various types:

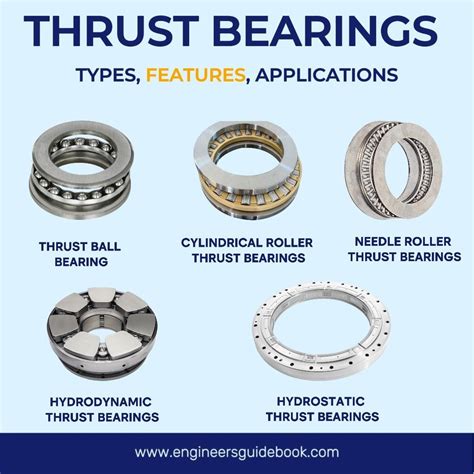
-
Plain Thrust Bearings: The simplest type, with a flat thrust washer and collar.
-
Tapered-Roller Thrust Bearings: Utilizes tapered rollers instead of washers for increased load capacity.
-
Ball Thrust Bearings: Employ bearing balls between the washer and collar, offering lower friction.
-
Spherical Roller Thrust Bearings: Designed for exceptionally heavy loads, featuring self-aligning spherical rollers.
-
Hydrodynamic Thrust Bearings: Employs a pressurized fluid film to support the axial load, reducing friction and heat generation.
Applications of Thrust Bearings
Thrust bearings find widespread applications in industries such as:
-
Power Generation: Supporting turbines, generators, and pumps.
-
Aerospace: Used in aircraft engines, propellers, and helicopter rotor systems.
-
Automotive: Found in transmissions, differentials, and steering systems.
-
Steel Industry: Employed in rolling mills and other machinery involving high axial loads.
-
Wind Turbines: Supporting the main shaft and blades that generate electricity.
Design Considerations for Thrust Bearings
When designing thrust bearings, several factors need to be considered:
-
Load Capacity: Determine the maximum axial load that the bearing must support.
-
Speed: Account for the rotational or oscillatory speed of the bearing.
-
Friction: Minimize friction to reduce power loss and wear.
-
Lubrication: Select a suitable lubricant to reduce friction and extend bearing life.
-
Materials: Choose materials with appropriate hardness, wear resistance, and corrosion resistance.
Maintenance of Thrust Bearings
Regular maintenance is crucial to ensure optimal performance and lifespan of thrust bearings. Key maintenance practices include:
-
Lubrication: Monitor and replenish lubricant levels as recommended by the manufacturer.
-
Inspection: Periodically check for wear, damage, or contamination.
-
Alignment: Ensure proper alignment between bearing components to prevent excessive load or premature failure.
-
Temperature Monitoring: Monitor operating temperatures to prevent overheating and premature wear.
-
Replacement: Replace worn or damaged bearings in a timely manner to avoid catastrophic failure.
Common Issues and Troubleshooting
Thrust bearings can experience various issues that require troubleshooting and repair. Common problems include:
-
Wear: Excessive wear on bearing surfaces due to insufficient lubrication or overloading.
-
Misalignment: Improper alignment leading to uneven load distribution and premature failure.
-
Contamination: Dirt, debris, or moisture entering the bearing, causing increased friction and wear.
-
Overheating: Excessive operating temperatures resulting from insufficient lubrication or overloading.
-
Corrosion: Chemical attack on bearing materials due to exposure to moisture or corrosive substances.
Case Studies and Lessons Learned
Case Study 1: A wind turbine experienced premature failure of thrust bearings in its gearbox. Investigation revealed that insufficient lubrication due to a faulty lubrication system led to increased friction and wear, resulting in bearing failure and downtime of the turbine.

Lesson Learned: Emphasizes the importance of proper lubrication and regular maintenance to prevent bearing failures.
Case Study 2: A large steel mill faced a persistent problem with thrust bearing failures in its rolling mill. Analysis showed that overloading was the cause of premature wear and failure. By redesigning the rolling mill to reduce axial loads, the issue was resolved.
Lesson Learned: Highlights the need to consider load capacity in bearing design and to avoid overloading bearings to ensure optimal performance.
Case Study 3: A power plant experienced extended maintenance downtime due to recurring thrust bearing failures in its generator. Root cause analysis revealed that improper alignment led to uneven load distribution, causing excessive wear and failure. By realigning the bearing components, the problem was solved.
Lesson Learned: Emphasizes the importance of proper alignment to ensure balanced load distribution and prevent premature failures.
Tips and Tricks for Thrust Bearing Maintenance
- Use high-quality lubricants recommended by the manufacturer.
- Regularly check lubricant levels and top up as needed.
- Inspect bearings visually for wear, damage, or contamination.
- If possible, use alignment tools to ensure proper alignment of bearing components.
- Monitor operating temperatures to prevent overheating.
- Keep the bearing area clean and free from debris and moisture.
Step-by-Step Approach to Thrust Bearing Replacement
-
Preparations:
- Ensure the equipment is de-energized and locked out.
- Gather necessary tools, replacement bearings, and lubricants.
-
Disassembly:
- Remove the shaft or housing containing the bearing.
- Carefully remove the old thrust bearing, noting its orientation.
-
Inspection:
- Inspect the old bearing for signs of wear, damage, or contamination.
- Examine the mating surfaces for any irregularities.
-
Cleaning and Preparation:
- Clean mating surfaces thoroughly using a solvent.
- Apply a thin layer of lubricant to the new bearing surfaces.
-
Installation:
- Carefully place the new bearing into the housing or on the shaft in the correct orientation.
- Secure the bearing using bolts, screws, or snap rings.
-
Reassembly:
- Reassemble the equipment, ensuring proper alignment.
- Tighten all bolts or screws to the manufacturer's specifications.
-
Lubrication:
- Lubricate the bearing according to the manufacturer's instructions.
-
Testing:
- Start the equipment and check that the bearing is operating smoothly without excessive noise or vibration.
Comparison of Thrust Bearing Types
Type |
Advantages |
Disadvantages |
Applications |
Plain Thrust Bearings |
Low cost, simple design |
Limited load capacity, high friction |
Light-duty applications |
Tapered-Roller Thrust Bearings |
High load capacity, long life |
Moderate cost, requires precise alignment |
Medium to heavy-duty applications |
Ball Thrust Bearings |
Low friction, low noise |
Limited load capacity, not suitable for high speeds |
Light to medium-duty applications |
Spherical Roller Thrust Bearings |
Extremely high load capacity, self-aligning |
High cost, large size |
Heavy-duty applications |
Hydrodynamic Thrust Bearings |
Minimal friction, low heat generation |
Complex design, requires external lubrication system |
High-speed applications |
Key Performance Indicators for Thrust Bearings
-
Load Capacity: Measured in kilonewtons (kN) or pounds-force (lbf), it indicates the maximum axial load the bearing can support.
-
Speed: Measured in revolutions per minute (RPM), it represents the maximum rotational or oscillatory speed the bearing can handle.
-
Friction Coefficient: A dimensionless value, it indicates the resistance to motion between bearing surfaces.
-
Wear Resistance: Measured in millimeters per hour (mm/h), it indicates the rate at which the bearing surfaces wear under load.
-
Temperature Rise: Measured in degrees Celsius (°C) or Fahrenheit (°F), it represents the increase in temperature due to friction and bearing operation.
-
Service Life: Measured in hours, it indicates the expected lifespan of the bearing under specified operating conditions.
Tables and Diagrams
Table 1: Load Capacities of Different Thrust Bearing Types
Type |
Load Capacity (kN) |
Plain Thrust Bearings |
10 - 100 |
Tapered-Roller Thrust Bearings |
50 - 1000 |
Ball Thrust Bearings |
15 - 300 |
Spherical Roller Thrust Bearings |
100 - 5000 |
Hydrodynamic Thrust Bearings |
50 - 10000 |
Table 2: Friction Coefficients of Different Thrust Bearing Types
Type |
Friction Coefficient |
Plain Thrust Bearings |
0.1 - 0.2 |
Tapered-Roller Thrust Bearings |
0.05 - 0.1 |
Ball Thrust Bearings |
0.02 - 0.05 |
Spherical Roller Thrust Bearings |
0.03 - 0.08 |
Hydrodynamic Thrust Bearings |
0.001 - 0.005 |
Diagram 1: Schematic of a Tapered-Roller Thrust Bearing
[Image of a tapered-roller thrust bearing]
Glossary of Terms
-
Axial Load: A load applied along the axis of the shaft or housing.
-
Friction: A force that opposes motion between two surfaces in contact.
-
Lubrication: The application of a substance to reduce friction and wear.
-
Preload: A controlled force applied to a bearing assembly to reduce play and improve performance.
-
Thrust Collar: A ring-shaped