Connecting Rod Bearings: The Essential Guide for Beginners and Experts Alike
Connecting rod bearings are crucial components in internal combustion engines, playing a pivotal role in ensuring smooth operation and extended engine life. These bearings facilitate the rotational motion of the connecting rods, which transmit power from the pistons to the crankshaft. Understanding the function, construction, maintenance, and troubleshooting of connecting rod bearings is essential for engine longevity and performance.
Understanding Connecting Rod Bearings: A Technical Deep Dive
Construction and Function
Connecting rod bearings typically consist of a thin layer of bearing material, such as white metal or copper alloy, bonded to a steel or aluminum backing. The bearing material provides a low-friction surface, minimizing wear and tear on the connecting rod and crankshaft.
The bearings are housed within the big end of the connecting rod, which connects to the crankshaft, and the small end, which attaches to the piston. Oil is supplied to the bearings through drilled passages in the crankshaft, ensuring continuous lubrication and cooling.
Types and Applications
There are two main types of connecting rod bearings:

-
Plain bearings: These have a simple cylindrical shape without grooves or other features. They are commonly used in lower-performance engines due to their low cost and ease of manufacture.
-
Roller bearings: These incorporate small rollers between the bearing material and the backing, allowing for reduced friction and higher load capacity. They are often found in high-performance engines due to their superior durability.
Maintenance and Troubleshooting of Connecting Rod Bearings
Regular Maintenance
To ensure optimal performance and longevity of connecting rod bearings, regular maintenance is crucial. Key maintenance tasks include:

- Periodic oil changes: Fresh oil contains additives that reduce friction and prevent corrosion, protecting the bearings and other engine components.
- Oil filter replacement: The oil filter traps debris and contaminants, preventing them from reaching the bearings and causing damage.
- Inspection for wear: Bearings should be inspected regularly for any signs of wear, such as scoring, pitting, or excessive clearance. Worn bearings should be replaced promptly to prevent further damage.
Troubleshooting Common Problems
Connecting rod bearing problems typically manifest as unusual noises or performance issues. Common problems include:
-
Knocking or tapping noises: This can indicate excessive bearing clearance, caused by worn bearings or insufficient oil pressure.
-
Engine overheating: Worn or damaged bearings can generate excessive friction, leading to increased heat and potentially engine overheating.
-
Reduced engine power: Severely worn or damaged bearings can hinder the transfer of power from the pistons to the crankshaft, resulting in reduced engine performance.
Tips and Tricks for Maximizing Connecting Rod Bearing Life
-
Use high-quality oil: Synthetic oils offer superior lubrication and protection compared to conventional oils.
-
Maintain proper oil pressure: Insufficient oil pressure can lead to bearing damage. Ensure the oil pressure gauge reads within the specified range.
-
Avoid extended high-RPM operation: Excessive engine speed can increase bearing wear and reduce their lifespan.
-
Monitor oil temperature: High oil temperatures can compromise lubrication and accelerate bearing wear. Address any issues that cause excessive oil heating.
Common Mistakes to Avoid: A Pitfall Guide
-
Neglecting oil changes: Failure to change oil regularly can result in contaminated oil that damages bearings.
-
Installing the wrong bearings: Using bearings with incorrect dimensions or tolerances can lead to premature wear or even catastrophic engine failure.
-
Improper bearing lubrication: Insufficient lubrication can cause dry running and bearing failure. Ensure proper oil flow to the bearings.
-
Ignoring bearing performance issues: Knocking noises or engine overheating should be addressed immediately, as they can indicate bearing problems that, if neglected, can lead to severe engine damage.
Step-by-Step Guide to Connecting Rod Bearing Replacement
Replacing connecting rod bearings requires mechanical expertise and precision. Follow these steps carefully:
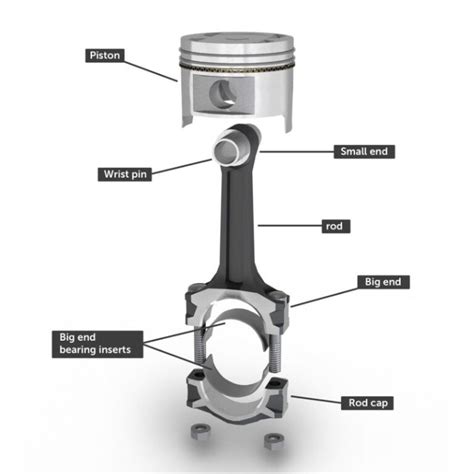
-
Disassemble the engine: Remove the cylinder head, oil pan, and crankshaft.
-
Inspect the bearings: Examine the bearings for wear or damage. Replace any worn or damaged bearings.
-
Lubricate the bearings: Apply a thin layer of engine oil to the new bearings.
-
Install the bearings: Place the bearings in their respective positions in the connecting rods and crankshaft.
-
Tighten the bolts: Use a torque wrench to tighten the bolts holding the bearings in place, following the specified torque values.
-
Reassemble the engine: Replace the crankshaft, oil pan, and cylinder head, following proper procedures.
Conclusion: The Cornerstone of Engine Performance and Longevity
Connecting rod bearings are vital components that play an indispensable role in engine operation and durability. Understanding their construction, function, maintenance, and troubleshooting is paramount for keeping engines running smoothly and extending their lifespan. By adhering to proper maintenance practices, avoiding common pitfalls, and following the step-by-step guide for replacement, you can ensure the optimal performance of your engine's connecting rod bearings.
Additional Resources
- Society of Automotive Engineers (SAE): https://www.sae.org/
- American Bearing Manufacturers Association (ABMA): https://www.abma.org/
- National Institute of Standards and Technology (NIST): https://www.nist.gov/
Table 1: Connecting Rod Bearing Materials
Material |
Properties |
Applications |
White metal |
Low friction, high conformability |
Low-load, low-RPM engines |
Copper alloy |
High strength, good heat resistance |
Medium-load, medium-RPM engines |
Steel |
High load capacity, low friction |
High-load, high-RPM engines |
Table 2: Connecting Rod Bearing Types
Type |
Advantages |
Disadvantages |
Plain bearings |
Low cost, simple design |
Limited load capacity, higher friction |
Roller bearings |
High load capacity, reduced friction |
More expensive, more complex design |
Table 3: Connecting Rod Bearing Maintenance Schedule
Maintenance Task |
Frequency |
Oil change |
Every 5,000-10,000 miles |
Oil filter replacement |
Every 5,000-10,000 miles |
Bearing inspection |
Every 50,000-100,000 miles |