Connecting Rod Bearings: The Essential Guide
Connecting Rod Bearings: The Key to Engine Performance
Connecting rod bearings are essential components that play a crucial role in the efficient operation of an engine. These bearings allow for smooth and reliable movement between the connecting rod and the crankshaft, ensuring optimal engine performance and longevity. Failure to maintain or replace worn-out connecting rod bearings can lead to catastrophic engine damage.
Understanding Connecting Rod Bearings
Function
Connecting rod bearings act as a barrier between the connecting rod and the crankshaft, allowing for rotational motion without excessive friction. The bearings are typically made of a thin layer of bearing material, such as copper-lead or aluminum alloy, bonded to a steel backing. This material provides a low-friction surface and reduces wear on the connecting rod and crankshaft.
Design
Connecting rod bearings come in two halves: the upper bearing and the lower bearing. They are designed to fit snugly around the crankshaft journal and the connecting rod big end, respectively. The bearings are held in place by a bearing cap, which is bolted to the connecting rod.


Types
There are two main types of connecting rod bearings:
-
Plain bearings: These bearings have a simple cylindrical shape and rely on a thin layer of oil to separate the contacting surfaces.
-
Rolling element bearings: These bearings utilize small rollers or balls between the bearing races to reduce friction.
Importance of Connecting Rod Bearings
Connecting rod bearings are vital to engine performance for several reasons:
Reduce Friction
Bearings minimize friction between moving parts, allowing the engine to operate smoothly and efficiently. By reducing friction, bearings also help to improve fuel economy and minimize engine wear.
Maintain Oil Pressure
Bearings help to maintain oil pressure in the engine by creating a seal between the crankshaft and the connecting rod. This oil pressure lubricates the bearings and other engine components, preventing premature wear and failure.
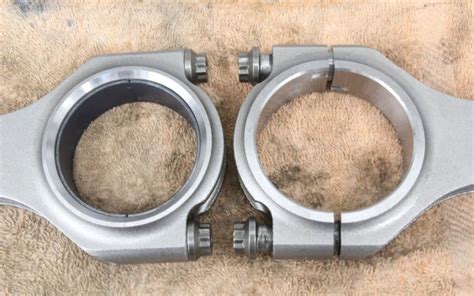
Dampen Vibrations
Bearings absorb vibrations generated by the engine's combustion process. This helps to reduce noise and minimize the transmission of vibrations to the rest of the engine and vehicle.

Signs of Worn Connecting Rod Bearings
Worn connecting rod bearings can cause a variety of symptoms, including:
-
Knocking or tapping noise: This noise is caused by excessive clearance between the bearings and the crankshaft journal or connecting rod big end.
-
Loss of oil pressure: Worn bearings can allow oil to leak from the engine, resulting in a loss of oil pressure.
-
Engine overheating: Overheated bearings can lead to a loss of lubrication, increased friction, and a rise in engine temperature.
-
Reduced engine performance: Worn bearings can cause the engine to run sluggishly and lose power.
Causes of Connecting Rod Bearing Failure
Connecting rod bearing failure can be caused by several factors, including:
-
Lack of lubrication: Insufficient or contaminated oil can lead to increased friction and premature bearing failure.
-
Overheating: Excessive engine temperatures can lead to bearing failure due to thermal expansion and loss of lubrication.
-
Excessive loads: Heavy loads or sudden engine acceleration can put excessive stress on bearings, leading to damage.
-
Defective bearings: Manufacturing defects or poor material quality can cause bearings to fail prematurely.
-
Improper installation: Incorrectly installed bearings can lead to misalignment and early failure.
Effective Strategies for Connecting Rod Bearing Maintenance
-
Follow Regular Maintenance: Adhere to the manufacturer's recommended maintenance schedule for oil changes and filter replacements.
-
Use High-Quality Oil: Choose high-quality engine oil that meets the manufacturer's specifications.
-
Monitor Oil Pressure: Regular monitoring of oil pressure helps to detect any abnormal drops that may indicate worn bearings.
-
Listen for Unusual Noises: Pay attention to any knocking or tapping noises that may be indicative of bearing problems.
-
Inspect Bearings Regularly: During engine inspections, carefully examine the connecting rod bearings for signs of wear or damage.
Tips and Tricks
-
Cleanliness is Crucial: When handling bearings, ensure that your hands and the work area are clean to prevent contamination.
-
Use Proper Tools: The correct tools, such as torque wrenches and bearing pullers, are essential for proper installation and removal.
-
Lubricate Bearings Thoroughly: Apply a thin layer of engine oil to the bearings before installation to ensure proper lubrication from the start.
-
Tighten Bearings Properly: Follow the manufacturer's torque specifications for connecting rod bearing bolts to prevent overtightening or undertightening.
-
Break-In New Bearings Properly: After installing new bearings, allow the engine to run at varying speeds for a break-in period to ensure proper seating and wear-in.
Common Mistakes to Avoid
-
Overlooking Oil Changes: Negligence with oil changes can lead to bearing failure due to lack of lubrication.
-
Using Incorrect Oil: Using engine oil that doesn't meet the manufacturer's specifications can reduce bearing life.
-
Ignoring Knocking Noises: Ignoring knocking noises can lead to severe bearing damage and catastrophic engine failure.
-
Improper Bearing Installation: Incorrect installation techniques can misalign bearings and cause premature failure.
-
Overheating the Engine: Excessive engine temperatures can compromise bearing lubrication and lead to bearing failure.
Step-by-Step Approach to Connecting Rod Bearing Replacement
-
Safety First: Wear protective gear and ensure the vehicle is parked on a level surface with the parking brake engaged.
-
Remove Ancillary Components: Disconnect the battery, remove the intake manifold, and drain the oil.
-
Unbolt Connecting Rod Caps: Use a torque wrench to loosen and remove the connecting rod cap bolts.
-
Remove Worn Bearings: Carefully remove the upper and lower connecting rod bearings using a bearing puller.
-
Clean Bearing Surfaces: Clean the crankshaft journal and connecting rod big end thoroughly using a solvent and clean rags.
-
Inspect Surfaces: Examine the crankshaft journal and connecting rod big end for any damage or wear.
-
Install New Bearings: Lubricate the new bearings with engine oil and carefully insert them into place.
-
Reinstall Connecting Rod Caps: Apply thread sealant to the connecting rod cap bolts and tighten them to the manufacturer's torque specifications in a crisscross pattern.
-
Reassemble Engine: Reinstall the intake manifold, connect the battery, and fill the engine with fresh oil.
Call to Action
Connecting rod bearings are essential for engine performance and reliability. By following the tips and strategies outlined in this guide, you can extend the life of your bearings and ensure optimal engine operation. If you suspect any problems with your connecting rod bearings, do not hesitate to consult a qualified mechanic for diagnosis and repair. Remember, proper maintenance and care are key to a healthy and long-lasting engine.