Sliding Bearings: The Unsung Heroes of Mechanical Systems
Introduction
Sliding bearings, also known as plain bearings, are mechanical elements that support rotating or reciprocating loads by allowing relative motion between two surfaces. They play a crucial role in a wide range of machinery, comprising approximately 80% of all bearings used in industrial applications. This article delves into the intricacies of sliding bearings, exploring their types, applications, design considerations, and maintenance practices.
Types of Sliding Bearings
Sliding bearings come in various types, each tailored to specific operating conditions:

-
Journal bearings: Support a rotating shaft in a cylindrical bore.
-
Thrust bearings: Handle axial loads, preventing relative movement along the shaft axis.
-
Linear bearings: Guide and support reciprocating or linear motion.
-
Spherical bearings: Allow for motion in any direction, compensating for misalignment and tilt.
-
Hydrodynamic bearings: Utilize a thin film of fluid to separate the bearing surfaces, reducing friction and wear.
-
Hydrostatic bearings: Similar to hydrodynamic bearings, but use an external pressure source to maintain the fluid film.
Applications of Sliding Bearings
Sliding bearings find extensive use in diverse industries, including:

- Automotive engines and transmissions
- Industrial machinery (pumps, compressors, turbines)
- Aerospace components
- Construction equipment
- Medical devices
- Energy systems
Design Considerations for Sliding Bearings
Proper design of sliding bearings is essential for optimal performance and reliability. Key considerations include:
-
Bearing materials: Select materials with low friction, high wear resistance, and good fatigue strength. Common choices include babbitt, bronze, and polymer composites.
-
Clearance: The gap between the bearing surface and the mating component should be sufficient to allow for lubrication and prevent excessive wear.
-
Lubrication: Provide adequate lubrication to minimize friction and protect against wear. Lubricants can range from oils and greases to solid lubricants.
-
Surface finish: The bearing surfaces should have a smooth finish to minimize friction and prevent wear.
Maintenance of Sliding Bearings
Regular maintenance is crucial to extend the life of sliding bearings:
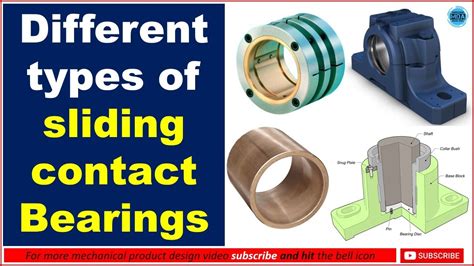
-
Lubrication monitoring: Check lubricant levels, quality, and contamination regularly.
-
Temperature monitoring: Excessive bearing temperatures indicate potential problems, such as lubrication failure or excessive loading.
-
Vibration monitoring: Unusual vibrations may indicate bearing misalignment, wear, or damage.
-
Periodic inspection: Dismantle and inspect the bearing regularly for signs of wear, pitting, or other defects.
Effective Strategies for Sliding Bearing Design
-
Material selection: Choose materials compatible with the operating environment, loads, and speeds.
-
Optimized clearance: Minimize clearance to reduce friction and wear while ensuring adequate lubrication.
-
Efficient lubrication: Ensure a constant supply of lubricant to the bearing surfaces.
-
Proper installation: Follow manufacturer's instructions carefully for proper alignment and preload.
-
Monitoring and maintenance: Implement a regular monitoring and maintenance program to prevent premature failure.
Common Mistakes to Avoid
-
Insufficient clearance: Can lead to high friction, wear, and potential seizure.
-
Excessive clearance: Reduces bearing stiffness and increases vibration issues.
-
Inadequate lubrication: Causes increased friction, heat generation, and premature wear.
-
Improper installation: Can lead to misalignment, uneven loading, and reduced bearing life.
-
Neglecting maintenance: Failure to monitor and maintain the bearing can result in catastrophic failure.
Step-by-Step Approach to Analyzing a Sliding Bearing
-
Define the operating conditions: Load, speed, temperature, and environmental factors.
-
Select the appropriate bearing type: Based on the operating conditions and required motion.
-
Determine bearing dimensions: Calculate the required clearance, bearing length, and diameter.
-
Select bearing materials: Consider wear resistance, friction coefficient, and compatibility with the lubricant.
-
Design the lubrication system: Ensure an adequate and consistent supply of lubricant.
-
Analyze the bearing: Check for stress, wear, and temperature distribution under operating conditions.
-
Optimize the design: Iterate on the design parameters to improve performance and durability.
Pros and Cons of Sliding Bearings
Pros:
- Lower cost compared to rolling element bearings
- Provide smoother, quieter operation
- Can accommodate higher loads and speeds
- Allow for misalignment and tilt
Cons:
- Higher friction compared to rolling element bearings
- Require regular maintenance and lubrication
- Can be susceptible to wear and seizure under harsh conditions
FAQs About Sliding Bearings
-
What is the primary difference between sliding and rolling element bearings?
Sliding bearings allow for direct contact between the bearing surfaces, while rolling element bearings use rolling elements to reduce friction.
-
What factors influence the choice of bearing material?
The operating load, speed, temperature, and environment all play a role in material selection.
-
How can I determine the optimal clearance for a sliding bearing?
Clearance should be sufficient to allow for lubrication flow while minimizing friction and wear.
-
What is the importance of lubrication in sliding bearings?
Lubrication reduces friction and wear, extends bearing life, and prevents seizure.
-
How do I monitor the condition of a sliding bearing?
Regularly monitor lubrication levels, temperature, and vibration to detect potential issues.
-
What are common causes of sliding bearing failure?
Inadequate lubrication, excessive clearance, improper installation, and harsh operating conditions can contribute to failure.
Humorous Anecdotes and Learning Points
-
The Engineer's Mishap: A well-intentioned engineer overtightened the bearing preload, mistaking it for a tightening bolt. The bearing seized within minutes, causing the machine to grind to a halt.
Lesson learned: Understand the purpose and limits of each component before making adjustments.
-
The Lubricant Odyssey: A maintenance technician accidentally used the wrong type of lubricant for a sliding bearing. The inappropriate lubricant caused the bearing to overheat and fail within a short period.
Lesson learned: Always use the manufacturer-specified lubricant and follow lubrication instructions meticulously.
-
The Misaligned Motor: A team of mechanics installed a motor with misaligned bearings. The motor vibrated excessively and made a loud noise, attracting the attention of the entire workshop.
Lesson learned: Proper bearing alignment is crucial for smooth and quiet operation of any machinery.
Reference Tables
Table 1: Types of Sliding Bearings and Applications
Bearing Type |
Applications |
Journal bearing |
Rotating shafts in automotive engines, pumps, and gearboxes |
Thrust bearing |
Axial loads in compressors, turbines, and clutches |
Linear bearing |
Reciprocating or linear motion in machine tools, packaging equipment, and medical devices |
Spherical bearing |
Motion in any direction in robotic joints, flight control systems, and aerospace applications |
Hydrodynamic bearing |
High-speed applications, such as gas turbines, steam turbines, and centrifugal pumps |
Hydrostatic bearing |
Precision applications, such as machine tool spindles, optical instruments, and biomedical devices |
Table 2: Bearing Materials and Their Properties
Material |
Advantages |
Disadvantages |
Babbitt |
Low friction, good conformability |
Low strength, requires a backing material |
Bronze |
High strength, good wear resistance |
Higher friction than babbitt, may require a coating |
Polymer composites |
Low friction, self-lubricating |
Lower strength and wear resistance than metallic materials |
Ceramic composites |
High wear resistance, low friction |
Expensive, brittle |
Table 3: Common Causes of Sliding Bearing Failure
Cause |
Description |
Inadequate lubrication |
Lack of sufficient lubricant to reduce friction and wear |
Excessive clearance |
Excessive gap between the bearing surfaces, leading to high friction and vibration |
Improper installation |
Misalignment, incorrect preload, or contamination during installation |
Harsh operating conditions |
Overloading, excessive temperature, or corrosive environment |
Wear and fatigue |
Gradual deterioration of bearing surfaces over time |