Roller Bearings: A Comprehensive Guide to Efficient Motion and Load Support
Table of Contents:
- Introduction
- Types of Roller Bearings
- Applications of Roller Bearings
- Advantages of Roller Bearings
- Disadvantages of Roller Bearings
- Design Considerations for Roller Bearings
- Lubrication of Roller Bearings
- Maintenance of Roller Bearings
- Failure Modes and Troubleshooting
- Interesting Stories About Roller Bearings
- Effective Strategies for Using Roller Bearings
- Common Mistakes to Avoid with Roller Bearings
- Step-by-Step Guide to Installing and Maintaining Roller Bearings
- Comparison of Roller Bearings with Other Bearing Types
- Frequently Asked Questions
Introduction:
Roller bearings play a pivotal role in modern machinery, providing efficient motion and load support. Their unique design consists of cylindrical rollers that rotate between inner and outer races, reducing friction and enabling heavy loads to be handled with minimal effort. This article delves into the diverse types, applications, advantages, and design considerations of roller bearings. Additionally, it offers insights into lubrication, maintenance, and troubleshooting, empowering engineers with the knowledge to optimize bearing performance and extend their lifespan.
Types of Roller Bearings:
Roller bearings are classified into several types, each with its own unique characteristics and applications. The primary types include:

1. Cylindrical Roller Bearings:
- Rollers are cylindrical in shape.
- Suitable for heavy radial loads and limited axial loads.
2. Tapered Roller Bearings:
- Rollers are tapered in shape.
- Capable of handling both radial and axial loads simultaneously.
3. Needle Roller Bearings:
- Rollers are slender and needle-like.
- Compact in size and can withstand high radial loads.

4. Spherical Roller Bearings:
- Rollers are concave on both sides.
- Can accommodate misalignment and support high radial and axial loads.
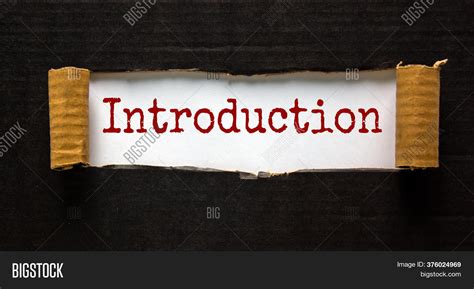
Applications of Roller Bearings:
Roller bearings are extensively used in a wide range of industrial and automotive applications, including:
- Machinery: Pumps, compressors, gearboxes
- Automotive: Transmissions, engines, wheel hubs
- Heavy equipment: Cranes, excavators, conveyors
- Aerospace: Turbines, landing gear
- Medical devices: Surgical equipment, prosthetics
Advantages of Roller Bearings:
-
High Load Capacity: Roller bearings can accommodate substantial loads due to their large contact area between the rollers and races.
-
Low Friction: The rolling motion of the cylindrical rollers results in minimal friction, reducing energy consumption.
-
Durability: Roller bearings are robust and have extended service lives under appropriate lubrication and maintenance conditions.
-
Versatility: The various types of roller bearings offer solutions for diverse applications, accommodating different load capacities, speeds, and precision requirements.
-
Cost-Effective: Roller bearings are readily available and cost-effective compared to other bearing types.
Disadvantages of Roller Bearings:
-
Limited Axial Load Capacity: Cylindrical roller bearings are primarily designed for radial loads and have limited axial load capabilities.
-
High Speed Limitations: Roller bearings may experience vibration and noise at high speeds due to their rolling action.
-
Sensitive to Contamination: Rollers and races must be protected from dirt and debris to prevent premature wear.
-
Noise: Roller bearings can generate some noise due to the rolling motion of the rollers.
-
Space Requirements: Roller bearings can be bulky compared to other bearing types, especially in smaller sizes.
Design Considerations for Roller Bearings:
When selecting and designing roller bearings, several key factors must be considered:
-
Load Capacity: Determine the radial and axial loads that the bearing will experience.
-
Speed: Consider the operating speed and the potential for vibration and noise.
-
Lubrication: Choose a lubricant that is compatible with the bearing materials and operating conditions.
-
Sealing: Protect the bearing from contamination by selecting appropriate seals.
-
Precision: Specify the desired precision level to ensure proper bearing function.
Lubrication of Roller Bearings:
Lubrication is crucial for roller bearing performance and longevity. Suitable lubricants include:
-
Oil Lubrication: Provides a protective film between rollers and races.
-
Grease Lubrication: Offers long-term lubrication and protects against contamination.
-
Solid Lubrication: Used in high-temperature or vacuum environments.
Maintenance of Roller Bearings:
Regular maintenance enhances bearing performance and extends lifespan. Practices include:
-
Inspection: Conduct periodic inspections for signs of wear or damage.
-
Cleaning: Remove dirt and debris to prevent contamination.
-
Re-lubrication: Replenish lubricant as recommended by the manufacturer.
Failure Modes and Troubleshooting:
Common failure modes in roller bearings include:
-
Wear: Abrasion or fatigue on rollers and races.
-
Overheating: Excessive friction or inadequate lubrication.
-
Noise and Vibration: Misalignment, contamination, or bearing damage.
-
Sealing Failure: Contamination ingress.
-
Corrosion: Exposure to moisture or harsh chemicals.
Interesting Stories About Roller Bearings:
-
The Roller Coaster Ride: A roller coaster experiences extreme loads and speeds, relying on precision roller bearings to ensure a smooth and safe ride.
-
The Windmill Whisperer: Wind turbines rely on massive roller bearings to support the weight of the rotor and enable it to rotate smoothly.
-
The Martian Rover: NASA's Mars rovers utilize advanced roller bearings to navigate the rugged Martian terrain and conduct scientific research.
Lesson Learned: Roller bearings are vital components in diverse applications, enabling smooth motion, supporting heavy loads, and ensuring reliability.
Effective Strategies for Using Roller Bearings:
- Use the appropriate type of roller bearing for the specific application.
- Select bearings with adequate load capacity and speed capabilities.
- Ensure proper lubrication and sealing to prevent premature wear.
- Conduct regular inspections and maintenance to maximize bearing lifespan.
- Consult with bearing manufacturers or experts for technical guidance.
Common Mistakes to Avoid with Roller Bearings:
- Overloading the bearing beyond its rated capacity.
- Using incorrect lubrication or inadequate lubrication intervals.
- Neglecting sealing and allowing contamination to enter the bearing.
- Ignoring noise or vibration as early indicators of problems.
- Installing the bearing improperly or without proper alignment.
Step-by-Step Guide to Installing and Maintaining Roller Bearings:
Installation:
- Clean the bearing and surrounding components.
- Apply lubricant to the bearing surfaces.
- Insert the bearing into its housing.
- Secure the bearing with retaining rings or lock nuts.
Maintenance:
- Inspect the bearing periodically for signs of wear or damage.
- Re-lubricate the bearing as recommended by the manufacturer.
- Clean the bearing and surrounding area to remove debris.
- Replace the bearing if necessary due to wear or damage.
Comparison of Roller Bearings with Other Bearing Types:
Bearing Type |
Advantages |
Disadvantages |
Roller Bearings |
High load capacity, low friction |
Limited axial load capacity, noise |
Ball Bearings |
Low noise, high speed |
Lower load capacity |
Plain Bearings |
No rolling elements, low cost |
Higher friction, shorter lifespan |
Frequently Asked Questions:
Q: What is the difference between a cylindrical roller bearing and a tapered roller bearing?
A: Cylindrical roller bearings handle heavy radial loads, while tapered roller bearings can handle both radial and axial loads.

Q: Can roller bearings be used in high-temperature applications?
A: Some roller bearings are designed for high-temperature operation with specialized materials and lubricants.
Q: How often should roller bearings be inspected?
A: The inspection interval depends on the application and operating conditions, but regular inspections are recommended.
Q: What causes roller bearings to fail?
A: Common causes of failure include wear, overheating, contamination, and improper lubrication.
Q: Can roller bearings be repaired?
A: It is generally not recommended to repair roller bearings, as replacement is typically more cost-effective and ensures optimal performance.
Q: What is the typical lifespan of roller bearings?
A: The lifespan of roller bearings varies depending on the application, operating conditions, and maintenance practices. However, they can generally be expected to operate for several years with proper care.
Conclusion:
Roller bearings play a critical role in a wide range of industries, providing efficient motion and reliable load support. Understanding their types, advantages, and limitations enables engineers to optimize bearing selection and design for specific applications. By following best practices for lubrication, maintenance, and troubleshooting, roller bearings can deliver long-lasting performance. As technology continues to advance, new and innovative roller bearing designs will emerge, pushing the boundaries of motion control and efficiency.