Unlocking Industrial Automation Excellence with Kawasaki Arm Robots: A Comprehensive Guide
Introduction
In the era of Industry 4.0, automation has become a cornerstone of modern manufacturing. Among the various automated systems, robotic arms stand out as indispensable tools, transforming production lines and driving efficiency to new heights. One prominent name in industrial robotics is Kawasaki, renowned for its cutting-edge industrial arm robots, which have revolutionized the industry.
This comprehensive guide delves into the realm of Kawasaki industrial arm robots, exploring their features, benefits, and applications. We will also delve into best practices, tips, and common mistakes to avoid, providing a valuable resource for anyone seeking to harness the power of robotics in their industrial operations.
Understanding Kawasaki Industrial Arm Robots
Kawasaki industrial arm robots are advanced mechatronic devices designed to perform complex and repetitive tasks in a wide range of industrial settings. These robots are equipped with sophisticated controllers, powerful motors, and precise joints that enable them to execute movements with accuracy and speed.

Types of Kawasaki Industrial Arm Robots
Kawasaki offers a diverse range of industrial arm robots to cater to various industry needs. The main types include:
-
Articulated Robots: These robots feature multiple rotating joints that provide extensive flexibility and reach.
-
SCARA Robots: Specifically designed for assembly and pick-and-place operations, SCARA robots excel in high-speed, precision tasks.
-
Delta Robots: Ideal for applications requiring fast and accurate vertical movements, Delta robots utilize a parallel-link mechanism.
-
Collaborative Robots: These robots are designed to work safely alongside human operators, enhancing productivity and reducing the risk of accidents.
Key Features of Kawasaki Industrial Arm Robots
Kawasaki industrial arm robots are renowned for their exceptional performance, due to their incorporation of advanced features such as:
-
High Payload Capacity: Ranging from 2 kg to 1,500 kg, Kawasaki robots can handle a wide range of payloads, making them suitable for diverse applications.
-
Fast Cycle Times: These robots boast rapid cycle times, increasing productivity and throughput in manufacturing lines.
-
Exceptional Accuracy and Repeatability: Kawasaki robots deliver precise movements, ensuring consistent and reliable performance.
-
Advanced Controllers: Intuitive and user-friendly controllers simplify robot programming and operation, enhancing efficiency and reducing downtime.
-
Integrated Safety Systems: These robots include built-in safety features to prevent accidents and protect operators and equipment.
Benefits of Using Kawasaki Industrial Arm Robots
The integration of Kawasaki industrial arm robots into manufacturing operations offers numerous benefits:
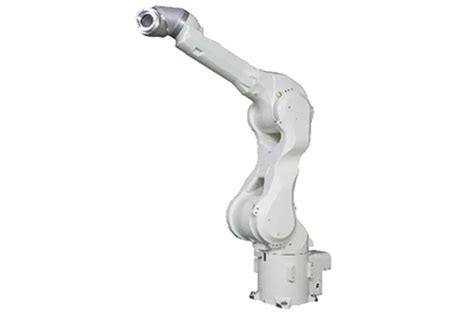
-
Increased Productivity: Robots work tirelessly 24/7, boosting production output and reducing labor costs.
-
Enhanced Quality: Robots perform tasks with precision and consistency, minimizing errors and improving product quality.
-
Reduced Labor Costs: Robots automate repetitive and labor-intensive tasks, freeing up human workers for more skilled and value-added roles.
-
Improved Safety: Robots remove the risk of workplace injuries associated with manual handling of heavy or hazardous materials.
-
Increased Flexibility: Robots can be reprogrammed to adapt to changing production demands, enhancing flexibility and responsiveness to market needs.
Applications of Kawasaki Industrial Arm Robots
Kawasaki industrial arm robots find widespread applications in various industry sectors, including:

-
Automotive Manufacturing: Assembly, welding, and painting
-
Electronics Manufacturing: Assembly, soldering, and testing
-
Food and Beverage: Packaging, handling, and inspection
-
Pharmaceuticals: Dispensing, filling, and packaging
-
Metalworking: Welding, cutting, and bending
-
Logistics and Warehousing: Order picking, sorting, and packing
Best Practices for Kawasaki Industrial Arm Robot Integration
To maximize the benefits of Kawasaki industrial arm robots, it is essential to follow best practices during integration:
-
Define Clear Objectives: Establish specific goals for robot implementation, aligning it with overall business objectives.
-
Thorough Site Assessment: Evaluate the production environment, identify potential challenges, and design a suitable robot installation plan.
-
Optimal Robot Selection: Choose the most appropriate robot type and model based on payload capacity, reach, and required accuracy.
-
Skilled Programming: Leverage experienced robotic programmers to develop efficient and error-free robot programs.
-
Comprehensive Training: Provide thorough training to operators and maintenance personnel to ensure safe and effective robot operation.
Tips and Tricks for Kawasaki Industrial Arm Robot Optimization
-
Payload Optimization: Ensure the payload is evenly distributed to minimize stress on the robot joints.
-
Motion Planning: Optimize robot movements to reduce cycle times while maintaining accuracy.
-
Preventive Maintenance: Implement a regular maintenance schedule to prevent unexpected breakdowns and extend robot lifespan.
-
Regular Software Updates: Keep robot software up-to-date to access the latest features and enhancements.
-
Continuous Improvement: Monitor robot performance and identify areas for improvement to maximize efficiency and productivity.
Common Mistakes to Avoid with Kawasaki Industrial Arm Robots
To prevent potential issues and maximize robot performance, avoid common mistakes:
-
Overloading the Robot: Exceeding the robot's payload capacity can damage the joints and reduce accuracy.
-
Improper Programming: Poorly written programs can lead to robot malfunctions or collisions.
-
Lack of Safety Measures: Ignoring safety guidelines increases the risk of accidents and injury.
-
Neglecting Maintenance: Failing to perform regular maintenance can result in premature robot failure and downtime.
-
Insufficient Operator Training: Untrained operators can make errors that compromise robot performance and safety.
Step-by-Step Approach to Kawasaki Industrial Arm Robot Integration
Follow these steps for successful Kawasaki industrial arm robot integration:
-
Assessment and Planning: Conduct a thorough assessment of your production needs and develop a detailed implementation plan.
-
Robot Selection: Choose the appropriate robot type and model based on your requirements.
-
Installation and Setup: Install the robot according to the manufacturer's guidelines and configure it for your specific application.
-
Programming and Testing: Develop and test robot programs to ensure proper functionality and safety.
-
Operator Training: Provide comprehensive training to operators to ensure safe and efficient robot operation.
-
Maintenance and Support: Establish a preventive maintenance schedule and access support resources to minimize downtime and maximize robot lifespan.
Why Kawasaki Industrial Arm Robots Matter
Kawasaki industrial arm robots are invaluable assets in modern manufacturing due to:
-
Enhanced Productivity: Robots significantly increase output by working tirelessly without breaks or fatigue.
-
Improved Quality: Robots perform tasks with precision and consistency, reducing errors and enhancing product quality.
-
Labor Cost Savings: Robots automate labor-intensive tasks, freeing human workers for more skilled and value-added roles.
-
Increased Flexibility: Robots can be reprogrammed to adapt to changing production demands, enhancing responsiveness to market needs.
-
Improved Safety: Robots eliminate the risk of workplace injuries associated with manual handling of heavy or hazardous materials.
Benefits of Kawasaki Industrial Arm Robots
Organizations that have integrated Kawasaki industrial arm robots have experienced numerous benefits, including:
-
Toyota: Achieved a 30% increase in productivity and reduced labor costs by 20% in its automotive assembly plant.
-
Nestlé: Enhanced product quality by 15% and reduced downtime by 25% in its food processing facility.
-
ABB: Improved efficiency by 20% and eliminated workplace accidents in its robotics manufacturing plant.
Humorous Stories and Lessons Learned
Story 1:
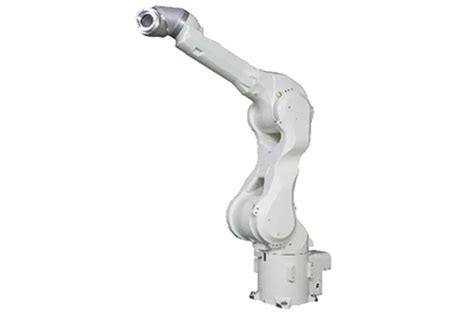
A Kawasaki robot was tasked with assembling delicate electronics components. However, due to a programming error, the robot mistook a worker's lunch sandwich for a component and proceeded to assemble it into the product. Lesson: Thoroughly test robot programs before deployment.
Story 2:
A Kawasaki robot was programmed to perform welding operations. However, a faulty sensor caused the robot to lose track of its position, resulting in a series of welds resembling a abstract art masterpiece on the workpiece. Lesson: Implement robust safety systems and regularly calibrate robot sensors.
Story 3:
A Kawasaki robot was tasked with handling heavy materials in a warehouse. Unfortunately, an inexperienced operator overloaded the robot, causing it to collapse and create a comical scene. Lesson: Ensure proper training and enforce payload limitations.
Effective Strategies for Kawasaki Industrial Arm Robot Integration
-
Partner with Experienced Integrators: Collaborate with qualified system integrators to ensure seamless robot integration and maximize ROI.
-
Emphasize Operator Training: Invest in comprehensive training programs to equip operators with the skills to operate robots safely and efficiently.
-
Leverage Simulation and Emulation Tools: Utilize simulation and emulation software to test robot programs and optimize production processes before physical implementation.
-
Continuous Monitoring and Evaluation: Track robot performance metrics and conduct regular evaluations to identify areas for improvement and optimization.
-
Establish a Culture of Continuous Improvement: Encourage innovation and ongoing process refinement to maximize the benefits of robot integration.
Tips and Tricks for Kawasaki Industrial Arm Robot Optimization
-
Optimize Robot Movement: Analyze robot movements and identify opportunities to reduce cycle times without compromising accuracy.
-
Utilize Advanced Programming Features: Explore and implement advanced programming features, such as path planning and collision avoidance, to enhance robot performance.
-
Regularly Update Software and Firmware: Maintain the latest software and firmware versions to access new features and improve robot reliability.
-
Consider Collaborative Robots: For tasks that require human-robot interaction, consider deploying collaborative robots to enhance flexibility and productivity.
-
Monitor Robot Health: Employ condition monitoring systems to identify potential issues and schedule preventive maintenance accordingly.
Common Mistakes to Avoid with Kawasaki Industrial Arm Robots
-
Underestimating Programming Complexity: Robot programming can