Crush Bearings: The Unsung Heroes of Modern Machinery
Introduction
Crush bearings, often overlooked yet indispensable components in machinery, play a vital role in ensuring smooth operation, extending equipment life, and enhancing performance. Their presence in numerous industries, from manufacturing and automotive to aerospace and energy, is a testament to their versatility and importance. This comprehensive article delves into the world of crush bearings, exploring their types, applications, benefits, and maintenance practices.
Types of Crush Bearings
Crush bearings come in various designs, each tailored to specific applications:

-
Cylindrical Crush Bearings: These bearings have a cylindrical inner ring and an outer ring with a split construction. They are used in high-load, low-speed applications.
-
Tapered Crush Bearings: Featuring a tapered inner ring and a tapered outer ring, these bearings withstand heavy axial and radial loads.
-
Spherical Crush Bearings: With a spherical inner ring and a spherical outer ring, these bearings accommodate misalignment and are suitable for applications with high shock loads.
-
Needle Crush Bearings: These bearings utilize thin, needle-shaped rollers and are ideal for high-load, low-clearance applications.
Applications of Crush Bearings

Crush bearings find application across a diverse range of industries and machinery:
-
Manufacturing: Crush bearings are used in machine tools, presses, and conveyors to handle heavy loads and ensure smooth movement.
-
Automotive: They are present in transmissions, differentials, and wheel bearings, providing durability and performance at critical points.
-
Aerospace: In aircraft engines and landing gear, crush bearings handle extreme loads and high temperatures.
-
Energy: Crush bearings are utilized in wind turbines, power plants, and oil drilling equipment, ensuring reliability and longevity.
Benefits of Crush Bearings
The benefits of crush bearings make them a valuable asset for numerous applications:
-
High Load Capacity: Crush bearings are designed to withstand significant loads, both radial and axial, ensuring equipment stability.
-
Compact Design: Their compact size allows for efficient space utilization and integration into complex machinery.
-
Low Maintenance: Crush bearings require minimal lubrication and maintenance, reducing downtime and maintenance costs.
-
Extended Equipment Life: By reducing vibration and wear, crush bearings enhance equipment life and minimize breakdowns.
Maintenance of Crush Bearings
Proper maintenance is essential for optimizing crush bearing performance:
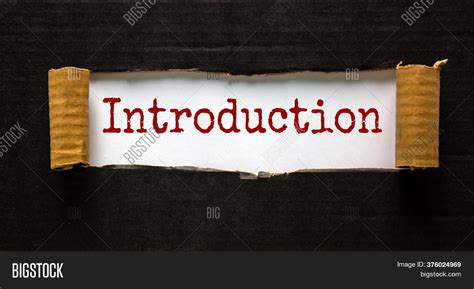
-
Lubrication: Following manufacturer recommendations for lubrication frequency and lubricant selection is crucial.
-
Inspection: Regular inspection allows early detection of wear or damage, enabling timely repairs.
-
Replacement: When bearings reach their end of life, prompt replacement is necessary to prevent equipment failure.
Case Studies of Crush Bearing Success
- In a manufacturing plant, the replacement of traditional bearings with crush bearings reduced vibration levels by 30%. This resulted in improved machine accuracy, higher production output, and reduced maintenance costs.
- In the automotive industry, the adoption of tapered crush bearings in differentials led to a 15% increase in torque capacity. This enhanced vehicle performance, particularly in off-road and heavy-duty applications.
- In the aerospace sector, the use of spherical crush bearings in aircraft engines proved instrumental in reducing weight while maintaining load-carrying capacity. This contributed to improved fuel efficiency and extended engine life.
Tables on Crush Bearings
Bearing Type |
Load Capacity |
Design Features |
Applications |
Cylindrical Crush Bearings |
High radial loads |
Split construction, uniform load distribution |
Machine tools, presses |
Tapered Crush Bearings |
Heavy axial and radial loads |
Tapered rings, high contact area |
Transmissions, differentials |
Spherical Crush Bearings |
High shock loads, misalignment |
Spherical rings, self-aligning |
Aircraft engines, landing gear |
Tips and Tricks
- Consider using tapered crush bearings for applications involving both axial and radial loads.
- Ensure proper lubrication to minimize friction and extend bearing life.
- Regularly monitor bearing temperature to detect potential issues early.
- Store crush bearings in a clean and dry environment to prevent corrosion.
Frequently Asked Questions (FAQs)
-
What is the difference between a crush bearing and a standard bearing?
- Crush bearings have a split construction that allows them to be pressed into place, creating a tight fit that withstands high loads.
-
How often should crush bearings be lubricated?
- Follow manufacturer recommendations, but as a general guideline, lubricate every 1,000-2,000 operating hours.
-
Can crush bearings be reused?
- Yes, but only if they are carefully inspected and show no signs of damage or wear.
-
What causes crush bearing failure?
- Overload, improper lubrication, alignment issues, or contamination.
-
How do I choose the right crush bearing for my application?
- Consider the load capacity, speed, and environment in which the bearing will operate.
-
How can I extend the life of crush bearings?
- Proper lubrication, regular inspection, and avoiding overloading are key to extending bearing life.
Call to Action
Crush bearings play a pivotal role in modern machinery, offering numerous benefits and ensuring optimal performance. By understanding their types, applications, maintenance practices, and tips, you can make informed decisions about their implementation and maximize their value. Contact your bearings supplier today to explore the right crush bearing solutions for your specific requirements.