The Genesis of Industrial Automation: Unveiling the First Industrial Robot
Introduction
The advent of the industrial robot has revolutionized the manufacturing industry, automating tasks that once required human labor. The journey towards this technological marvel began with a pioneering invention that set the stage for advancements to come. Join us as we delve into the annals of history to uncover the fascinating story of the first industrial robot.
The Birth of Unimate
In the year 1954, George Devol, an American inventor, laid the foundation for industrial automation with his groundbreaking concept of a programmable robotic arm. This vision materialized in 1956 when Devol and Joseph Engelberger established Unimation, the company credited with manufacturing and selling the first industrial robot.
Unimate, the brainchild of Devol and Engelberger, debuted in 1961 at General Motors' Trenton plant in New Jersey. This revolutionary machine was designed to perform repetitive tasks on an assembly line, replacing human welders. Weighing approximately 1.8 tons, Unimate was capable of lifting 50 pounds and could be programmed to perform a sequence of movements.
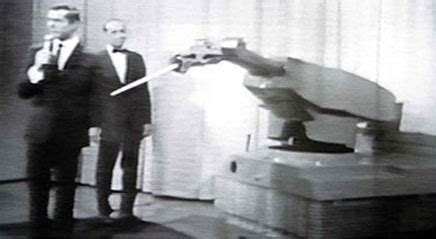
Unimate's Impact
Unimate's introduction marked a pivotal moment in manufacturing history. Its ability to automate dangerous and repetitive tasks not only increased productivity but also enhanced worker safety. The success of Unimate paved the way for the development of more sophisticated industrial robots, transforming the face of the manufacturing sector.
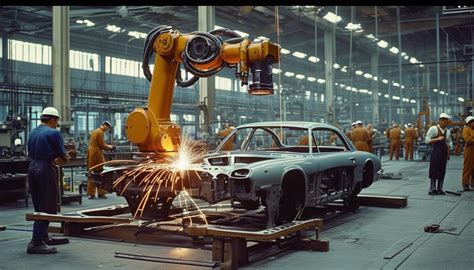
Evolution of Industrial Robotics
Since its inception, industrial robotics has undergone remarkable advancements. Today, these machines are equipped with advanced sensors, controllers, and artificial intelligence, enabling them to perform complex tasks with precision and efficiency.
Key Milestones
-
1970s: The introduction of microprocessors revolutionized robot control, allowing for greater flexibility and adaptability.
-
1980s: The development of computer-aided design (CAD) software enabled robots to be programmed offline, reducing downtime and improving accuracy.
-
1990s: The advent of industrial Ethernet allowed robots to be easily integrated with other factory equipment and systems.
-
21st Century: The emergence of collaborative robots, designed to work safely alongside human operators, is expanding the possibilities of human-robot collaboration.
Industrial Robot Applications
Industrial robots are now widely employed in a vast array of manufacturing and non-manufacturing industries. Their versatility enables them to automate a diverse range of tasks, including:

- Welding and assembly
- Material handling
- Painting and finishing
- Machine loading and unloading
- Inspection and testing
Economic Impact
The proliferation of industrial robots has had a significant economic impact. According to the International Federation of Robotics (IFR), there were approximately 3.5 million industrial robots operating worldwide in 2021, with an estimated 1.4 million units sold that year alone. The IFR predicts that the global stock of industrial robots will reach 7.4 million units by 2025, driven by the growing demand for automation in emerging economies.
Benefits for Manufacturers
Industrial robots offer numerous advantages for manufacturers, including:
-
Increased productivity: Robots can work 24/7, eliminating downtime and increasing output.
-
Improved quality: Robots perform tasks with consistent precision, reducing defects and enhancing product quality.
-
Reduced labor costs: Robots can replace human workers in dangerous or repetitive tasks, freeing up employees for more value-added activities.
-
Enhanced safety: Robots can perform tasks that are hazardous or ergonomically challenging for human workers, improving workplace safety.
Social Impact
While industrial robots have undoubtedly transformed the manufacturing sector, their impact on society as a whole is more nuanced.
Job Displacement
Some argue that the increased use of industrial robots will lead to widespread job displacement in the manufacturing industry. However, studies have shown that the introduction of robots often creates new jobs in engineering, maintenance, and other related fields.
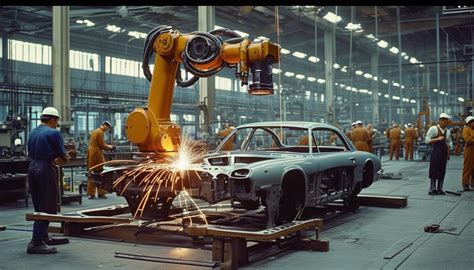
Skill Gap
The rapid advancements in robotics and automation have created a demand for skilled workers who can operate, maintain, and program these machines. Addressing the skills gap is crucial for ensuring that the benefits of industrial robotics are fully realized.
Ethical Considerations
As industrial robots become more sophisticated, ethical considerations arise regarding their role in society. These include:
-
Safety: Ensuring the safe operation of robots is paramount to prevent accidents and protect workers.
-
Liability: Determining responsibility in the event of an accident involving a robot is essential.
-
Job displacement: Mitigating the negative effects of job displacement caused by automation is a societal concern.
The Future of Industrial Robotics
The future of industrial robotics is poised for continued growth and innovation. Emerging trends include:
-
Collaborative robots: Robots designed to work alongside human operators, enhancing safety and productivity.
-
Artificial intelligence: The integration of AI into robots is enabling them to learn, adapt, and make decisions autonomously.
-
Cloud-based robotics: Robots connected to the cloud can access real-time data and updates, improving performance and reducing downtime.
Humorous Anecdotes from the World of Industrial Robots
-
The Robot that Forgot its Place: A cleaning robot at a museum accidentally wandered into an exhibit of priceless artifacts, causing mild chaos among the visitors.
-
The Robot that Became a Social Butterfly: A collaborative robot at a manufacturing plant developed a peculiar habit of greeting employees with a friendly wave, becoming a popular attraction among the workers.
-
The Robot that Took a Vacation: A robot at a theme park malfunctioned during a performance, sending it on an impromptu adventure through the park, much to the amusement of the guests.
Lessons Learned
These amusing anecdotes highlight the importance of:
-
Proper programming: Ensuring that robots are correctly programmed to prevent unexpected behaviors.
-
Human-robot collaboration: Designing robots that can work safely and effectively alongside human operators.
-
Safety considerations: Implementing robust safety measures to prevent accidents and protect both humans and robots.
Tips and Tricks for Working with Industrial Robots
-
Understand the robot's capabilities: Familiarize yourself with the robot's payload, reach, and safety features.
-
Program the robot carefully: Test and validate your programs thoroughly before running them on the robot.
-
Monitor the robot during operation: Pay attention to any unusual noises or vibrations that could indicate a problem.
-
Perform regular maintenance: Follow the manufacturer's recommended maintenance schedule to keep the robot in optimal condition.
-
Train operators properly: Ensure that operators are fully trained on the robot's operation and safety procedures.
Common Mistakes to Avoid
-
Overloading the robot: Exceeding the robot's payload capacity can damage the robot or cause injury to operators.
-
Improper programming: Programming errors can lead to unpredictable robot behavior and potential accidents.
-
Neglecting safety procedures: Failing to follow proper safety procedures can put both humans and robots at risk.
-
Lack of maintenance: Poorly maintained robots are more likely to malfunction, leading to downtime and safety hazards.
-
Inadequate training: Untrained operators may not be able to operate the robot safely or effectively.
Step-by-Step Approach to Working with Industrial Robots
-
Assess the task: Determine if the task is suitable for automation using an industrial robot.
-
Select the right robot: Choose a robot with the appropriate payload, reach, and safety features for the task.
-
Install and program the robot: Install the robot according to the manufacturer's instructions and program it to perform the desired tasks.
-
Test and validate the program: Thoroughly test the program to ensure it operates correctly and safely.
-
Deploy the robot: Integrate the robot into the production process and monitor its performance.
-
Maintain and upgrade the robot: Regularly perform maintenance and apply software updates to keep the robot operating at optimal levels.
Why Industrial Robots Matter
Industrial robots are transforming the manufacturing industry by:
-
Increasing productivity: Robots can work 24/7, reducing downtime and increasing output.
-
Improving quality: Robots perform tasks with consistent precision, reducing defects and enhancing product quality.
-
Reducing labor costs: Robots can replace human workers in dangerous or repetitive tasks, freeing up employees for more value-added activities.
-
Enhancing safety: Robots can perform tasks that are hazardous or ergonomically challenging for human workers, improving workplace safety.
-
Driving innovation: Robots enable the development of new products and processes, fostering innovation within the manufacturing sector.
Benefits of Industrial Robots
Organizations that embrace industrial robotics experience numerous benefits, including:
Increased Efficiency
- Reduced production times
- Improved product quality
- Increased throughput
Reduced Costs
- Lower labor costs
- Reduced material waste
- Decreased maintenance expenses
Enhanced Safety
- Improved worker safety
- Reduced workplace accidents
- Ergonomically optimized workstations
Advanced Features of Industrial Robots
-
Multi-Axis Movement: Robots can move along multiple axes, providing greater flexibility and reach.
-
End-of-Arm Tooling: Robots can be equipped with a variety of end-of-arm tools for specific applications, such as welding, gripping, and painting.
-
Sensors and Vision Systems: Robots can use sensors and vision systems to detect objects, avoid obstacles, and ensure precise movements.
-
Collaborative Operation: Robots are designed to work safely alongside human operators, enhancing productivity and safety.
-
Artificial Intelligence: Robots are increasingly incorporating AI algorithms to learn, adapt, and make decisions autonomously