Tracing the Genesis of Industrial Robotics: A Historical Odyssey
Embarking on a journey through the annals of technology, we delve into the captivating narrative of industrial robots, a pivotal innovation that has revolutionized countless industries worldwide. At the heart of this transformative story lies the creation of the first industrial robot, a groundbreaking achievement that paved the way for the modern era of automation.
The Birth of an Industrial Pioneer
In 1954, the seeds of industrial robotics were sown at General Motors' Willow Run plant in Michigan, USA. As the automotive industry grappled with the need for increased efficiency and precision, engineers George Devol and Joseph Engelberger conceived a groundbreaking solution: a programmable, computer-controlled manipulator capable of automating repetitive tasks.
Meet Unimate, the Trailblazing Robot
Dubbed "Unimate," this pioneering device was a marvel of engineering, capable of performing a range of tasks, including welding, painting, and material handling. Through a combination of hydraulics, electronics, and computer programming, Unimate could execute complex motions with remarkable accuracy, setting a new standard for industrial automation.
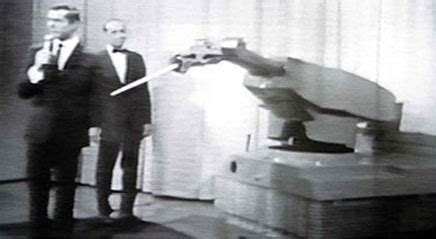
A Visionary Partnership
The entrepreneurial spirit of Devol and Engelberger drove them to establish Unimation, Inc., a company dedicated to developing and manufacturing industrial robots. With unwavering determination, they pushed the boundaries of robotics, introducing innovative technologies that would shape the future of manufacturing.

The Rise of Industrial Automation
The widespread adoption of industrial robots gained momentum in the 1970s and 1980s as industries across the globe recognized the transformative potential of automation. Robots were increasingly deployed in a diverse array of applications, including assembly, inspection, packaging, and welding.
Impact on Manufacturing
The integration of industrial robots into manufacturing processes brought about significant benefits, notably:
- Increased production efficiency and output
- Improved product quality and consistency
- Reduced labor costs and increased productivity
Furthermore, robots played a vital role in hazardous environments, performing tasks that were deemed unsafe for human workers.

Workforce Implications
The advent of industrial robots did not come without its challenges, particularly concerning the impact on workforce dynamics. Concerns were raised about potential job displacement and the need for specialized training to operate and maintain these advanced machines.
However, the long-term effects have been more nuanced, with robots complementing human workers rather than replacing them entirely. Instead, they have enabled workers to focus on higher-value tasks, contributing to increased productivity and innovation.
Evolution and Advancements
Since their inception, industrial robots have undergone continuous evolution, driven by technological advancements and the relentless pursuit of innovation. Key milestones in the evolution of industrial robotics include:
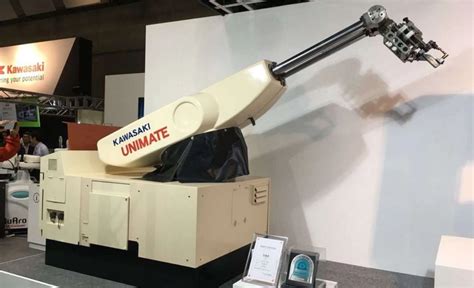
-
1973: Introduction of the first microprocessor-controlled robot, providing greater flexibility and programmability.
-
1980s: Emergence of sensory technologies, enabling robots to perceive and interact with their surroundings.
-
1990s: Development of collaborative robots, designed to work safely alongside human workers.
-
2000s: Introduction of cloud computing and artificial intelligence (AI), providing robots with advanced capabilities for data analysis and decision-making.
Current State of Industrial Robotics
Today, industrial robots are an integral part of modern manufacturing and other industries, with their presence spanning a wide range of sectors:
- Automotive
- Aerospace
- Electronics
- Food and beverage
- Healthcare
As of 2022, the global market for industrial robots is valued at approximately $50 billion, with a projected growth rate of 10% over the next decade.
Key Market Trends
Several key trends are shaping the current landscape of industrial robotics:
-
Increased adoption of collaborative robots: Robots designed to work alongside human workers, enabling a more flexible and efficient work environment.
-
Integration of AI and machine learning: Robots are becoming increasingly intelligent, capable of learning and adapting to changing environments.
-
Growing emphasis on data analytics: Robots are equipped with sensors and other technologies to collect and analyze data, providing valuable insights for process optimization.
Applications and Use Cases
Industrial robots are employed in a vast array of applications, including:
-
Assembly and manufacturing: Robots assemble products, handle materials, and perform welding and other tasks.
-
Inspection and testing: Robots inspect products for defects, verify quality, and perform non-destructive testing.
-
Packaging and palletizing: Robots package products, palletize goods, and perform other end-of-line tasks.
-
Material handling and logistics: Robots transport materials, automate warehousing operations, and perform other logistical functions.
-
Healthcare: Robots assist in surgery, dispense medications, and perform other tasks in healthcare settings.
Benefits of Industrial Robots
The adoption of industrial robots offers numerous benefits, including:
-
Increased productivity: Robots can operate 24/7, tirelessly performing tasks with consistent accuracy and speed.
-
Improved quality: Robots eliminate human error, leading to higher product quality and reduced defects.
-
Reduced costs: Robots can perform tasks more efficiently than humans, reducing labor costs and increasing overall profitability.
-
Enhanced safety: Robots can be deployed in hazardous environments or perform tasks that are dangerous for human workers.
-
Increased flexibility: Robots can be easily reprogrammed to perform different tasks, allowing for greater flexibility and adaptability in production processes.
Potential Drawbacks
While industrial robots offer numerous benefits, it is essential to consider potential drawbacks:
-
Initial investment cost: The upfront cost of acquiring and implementing industrial robots can be significant.
-
Training and maintenance: Robots require specialized training to operate and maintain, which can be an ongoing expense.
-
Job displacement: The introduction of robots may lead to job displacement for some workers, particularly in repetitive or low-skilled tasks.
-
Ethical concerns: The use of robots in certain applications raises ethical concerns, such as privacy and safety.
Tips and Tricks for Successful Implementation
For successful implementation of industrial robots, consider the following tips:
-
Thoroughly assess your needs: Define the specific tasks you need to automate and ensure that robots are a suitable solution.
-
Choose the right robot: Select the type of robot that best meets your performance, payload, and workspace requirements.
-
Invest in training: Provide adequate training to your staff to operate and maintain the robots effectively.
-
Monitor and optimize performance: Regularly monitor the performance of your robots and make adjustments as necessary to maximize efficiency.
-
Seek professional guidance: Consult with experienced professionals or robotics integrators to ensure proper implementation and support.
Common Mistakes to Avoid
When implementing industrial robots, avoid these common mistakes:
-
Underestimating the investment cost: Failing to account for the full cost of acquiring, installing, and maintaining robots can lead to budget overruns.
-
Poorly defined requirements: Not clearly defining the tasks to be automated can result in the selection of an unsuitable robot or improper implementation.
-
Lack of training: Inadequate training can lead to improper operation and maintenance, reducing the effectiveness of the robots.
-
Neglecting safety: Overlooking safety precautions can create hazards for workers and damage equipment.
-
Failure to monitor performance: Failing to regularly monitor the performance of robots can result in reduced efficiency and potential breakdowns.
Why Industrial Robotics Matters
The significance of industrial robotics extends beyond the realm of manufacturing and automation. These machines play a crucial role in:
-
Economic growth: Robots contribute to increased productivity, innovation, and global competitiveness.
-
Workforce empowerment: Robots enable workers to focus on higher-value tasks, leading to increased job satisfaction and career advancement opportunities.
-
Sustainability: Robots can reduce energy consumption, minimize waste, and improve environmental performance in manufacturing processes.
-
Healthcare advancements: Robots assist in life-saving surgeries, improve patient outcomes, and enhance the accessibility of healthcare services.
Potential Drawbacks and Ethical Considerations
While industrial robots offer undeniable benefits, it is essential to address potential drawbacks and ethical concerns associated with their use:
-
Job displacement: The adoption of robots in certain industries can lead to job displacement for low-skilled workers.
-
Safety concerns: Improperly designed or maintained robots can pose safety hazards to workers.
-
Privacy concerns: Robots equipped with sensors and cameras raise concerns about data collection and privacy侵犯.
-
Ethical dilemmas: The use of robots in certain applications, such as autonomous weapons, raises ethical questions about the boundaries of human responsibility.
Balancing Benefits and Drawbacks
To fully harness the benefits of industrial robots while mitigating potential drawbacks, consider the following principles:
-
Responsible implementation: Implement robots in a way that minimizes job displacement and maximizes the creation of new opportunities.
-
Ensuring safety: Establish and enforce rigorous safety standards to prevent accidents involving robots.
-
Protecting privacy: Implement measures to safeguard data collected by robots and respect the privacy of workers and consumers.
-
Addressing ethical concerns: Engage in ongoing dialogue about the ethical implications of robot use and establish clear guidelines for their responsible deployment.
Call to Action
The future of industrial robotics holds boundless possibilities. By embracing innovation, addressing challenges, and adopting best practices, we can harness the transformative power of these machines to enhance productivity, empower workers, and drive economic growth. Let us continue to explore the frontiers of robotics, ensuring that they serve as a catalyst for human progress and societal well-being.
Tables
Table 1: Historical Milestones in Industrial Robotics
Year |
Event |
1954 |
Invention of Unimate, the first industrial robot |
1973 |
Introduction of the first microprocessor-controlled robot |
1980s |
Emergence of sensory technologies for robots |
1990s |
Development of collaborative robots |