Unlocking the Potential of Mining Bell Bearing 2: A Comprehensive Guide
In the labyrinthine depths of the mining industry, the Mining Bell Bearing 2 stands as a pivotal component, orchestrating the seamless flow of materials. This invaluable device plays a critical role in enhancing productivity, ensuring safety, and optimizing operational efficiency. Delving into its intricacies, this comprehensive guide unravels the multifaceted potential of Mining Bell Bearing 2, empowering mining professionals with actionable insights.
Understanding Mining Bell Bearing 2
Mining Bell Bearings are highly specialized bearings designed to withstand the arduous conditions of mining operations, characterized by extreme loads, vibrations, and contaminants. Mining Bell Bearing 2 is a specific type of bearing that is engineered for use on conveyor systems, supporting the rotating shaft of the conveyor belt and ensuring smooth and efficient operation.
Key Features and Benefits
-
Robust Construction: Crafted from durable materials and featuring precision engineering, Mining Bell Bearing 2 boasts exceptional strength and longevity, ensuring reliable performance even under demanding workloads.
-
Low Friction Operation: The advanced design of Mining Bell Bearing 2 minimizes friction between rotating components, reducing energy consumption and extending bearing lifespan.
-
Self-Lubricating: These bearings are equipped with self-lubricating mechanisms, eliminating the need for manual lubrication, reducing maintenance downtime, and enhancing operational efficiency.
-
Sealed Housing: The sealed housing protects the bearing from external contaminants, such as dust, dirt, and moisture, ensuring long-term reliability in harsh mining environments.
Applications in Mining
Mining Bell Bearing 2 finds widespread applications in various mining operations, predominantly in the context of conveyor systems:
-
Conveyor Belt Support: These bearings provide critical support for the rotating shafts of conveyor belts, enabling the smooth and efficient transportation of materials from extraction sites to processing facilities.
-
Troughing Idlers: Mining Bell Bearing 2 is incorporated into troughing idlers, which shape the conveyor belt into a "trough" form, ensuring the stable and centered movement of materials.
-
Return Idlers: These bearings support the return section of the conveyor belt, facilitating the smooth rotation of the belt while minimizing friction and wear.
-
Head and Tail Pulleys: Mining Bell Bearing 2 is utilized in head and tail pulleys to support the rotating shafts of these pulleys, ensuring efficient belt tracking and preventing premature failure.
Maintenance Considerations
Proper maintenance is paramount to maximizing the performance and lifespan of Mining Bell Bearing 2. Regular inspections are essential to identify any potential problems, such as excessive wear, contamination, or misalignment. Preventive maintenance measures include:

-
Periodic Lubrication: While these bearings are self-lubricating, periodic lubrication may be necessary in highly abrasive or contaminated environments to supplement the self-lubricating mechanisms.
-
Bearing Replacement: When bearings reach the end of their service life, prompt replacement is crucial to prevent catastrophic failures and ensure continued operational efficiency.
-
Proper Alignment: Ensuring proper alignment of the bearings and other components of the conveyor system is essential to minimize wear and premature failure.
-
Storage and Handling: Proper storage and handling of spare bearings are important to prevent damage and ensure their optimal performance when needed.
Selecting the Right Mining Bell Bearing 2
Choosing the appropriate Mining Bell Bearing 2 for a specific application requires careful consideration of several key factors:
-
Load Capacity: The bearing must be capable of handling the anticipated loads imposed by the conveyor system and the materials being transported.
-
Speed Requirements: The bearing should be designed to operate at the desired conveyor belt speed while maintaining stability and efficiency.
-
Environmental Conditions: The bearing must be suitable for the specific environmental conditions of the mining operation, including exposure to dust, moisture, and extreme temperatures.
-
Compatibility: The bearing must be compatible with the other components of the conveyor system, including the shaft, housing, and seals.
Economic Benefits of Mining Bell Bearing 2
The implementation of Mining Bell Bearing 2 offers tangible economic benefits to mining operations:
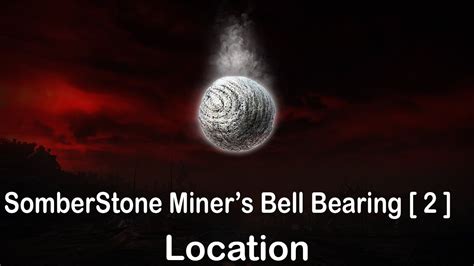
-
Reduced Maintenance Costs: Prolonged bearing lifespan and reduced maintenance downtime lead to significant savings in maintenance costs.
-
Increased Productivity: Optimized conveyor performance improves material flow, enhancing productivity and reducing operational bottlenecks.
-
Energy Savings: The low friction operation of these bearings minimizes energy consumption, resulting in reduced operating expenses.
-
Enhanced Safety: Reliable bearings ensure the smooth operation of conveyor systems, minimizing the risk of accidents and improving overall safety.
Inspiring Success Stories
-
The Conveyor Conundrum: A mining operation faced persistent conveyor belt failures due to premature bearing failure. After replacing the standard bearings with Mining Bell Bearing 2, the conveyor system experienced a remarkable increase in uptime, reducing downtime by over 40%.
-
The Efficiency Enigma: Another mine struggled with excessive energy consumption due to friction in the conveyor system. By utilizing Mining Bell Bearing 2, the mine achieved a 15% reduction in energy consumption, translating to substantial cost savings.
-
The Safety Savior: A conveyor belt incident at a mining site resulted in injuries to workers. An investigation revealed that worn-out bearings had caused the belt to derail. The subsequent replacement of all bearings with Mining Bell Bearing 2 significantly improved system reliability and enhanced safety.
Effective Strategies for Maximizing Performance
-
Regular Maintenance: Implement a comprehensive maintenance plan tailored to the specific operating conditions.
-
Proper Installation and Alignment: Ensure precise installation and alignment of bearings to minimize premature wear and failure.
-
Optimal Lubrication: Supplement self-lubricating mechanisms with periodic lubrication in challenging environments.
-
Condition Monitoring: Utilize condition monitoring techniques to detect potential issues early, enabling proactive maintenance.
-
Training: Provide comprehensive training to maintenance personnel on proper bearing handling, installation, and maintenance practices.
Compare Pros and Cons
Feature |
Pros |
Cons |
Robust Construction |
Exceptional strength and durability |
High initial investment cost |
Low Friction Operation |
Reduced energy consumption, extended bearing life |
May require specialized installation techniques |
Self-Lubricating |
Reduced maintenance downtime, enhanced operational efficiency |
Lubrication may be necessary in extreme conditions |
Sealed Housing |
Protection from contaminants, prolonged reliability |
Limited access for inspection and maintenance |
Frequently Asked Questions (FAQs)
Q: What are the key factors to consider when selecting a Mining Bell Bearing 2?
A: Load capacity, speed requirements, environmental conditions, and compatibility.

Q: How often should Mining Bell Bearing 2 be maintained?
A: Regular inspections and preventive maintenance should be conducted based on operating conditions and manufacturer recommendations.
Q: What is the expected lifespan of a Mining Bell Bearing 2?
A: With proper maintenance, Mining Bell Bearing 2 can last several years in demanding mining applications.
Useful Tables
Table 1: Specifications of Mining Bell Bearing 2
Specification |
Range |
Load Capacity |
500 - 20,000 kN |
Speed Limit |
50 - 200 rpm |
Temperature Range |
-20°C to 120°C |
Housing Material |
Cast Iron, Steel |
Table 2: Economic Benefits of Mining Bell Bearing 2
Benefit |
Impact |
Reduced Maintenance Costs |
20-40% savings |
Increased Productivity |
Up to 15% improvement |
Energy Savings |
10-20% reduction |
Enhanced Safety |
Minimize accidents related to conveyor failure |
Table 3: Maintenance Schedule for Mining Bell Bearing 2
Maintenance Task |
Frequency |
Visual Inspection |
Monthly |
Lubrication |
Quarterly or as per manufacturer's recommendations |
Bearing Replacement |
Every 2-5 years or as per condition monitoring data |
Alignment Check |
Every 6-12 months |