Thrust Bearings: The Cornerstone of Rotary Motion
In the realm of engineering, where precision and efficiency reign supreme, thrust bearings stand as unsung heroes. These remarkable devices play a pivotal role in countless applications, from towering wind turbines to high-speed rail networks. Their ability to manage axial loads with unparalleled reliability has transformed industries and revolutionized the way we harness energy.
Delving into the World of Thrust Bearings
Thrust bearings are specialized bearings engineered to withstand axial forces, which are forces acting parallel to the axis of rotation. Unlike radial bearings, which handle radial loads perpendicular to the axis, thrust bearings excel in managing thrust loads. This unique capability makes them indispensable in applications where axial loads are prevalent.
Types of Thrust Bearings and Their Applications
The world of thrust bearings encompasses a diverse range of types, each tailored to specific performance requirements. From ball thrust bearings and roller thrust bearings to tapered roller thrust bearings, the choice of bearing type depends on factors such as load capacity, speed, and environmental conditions.
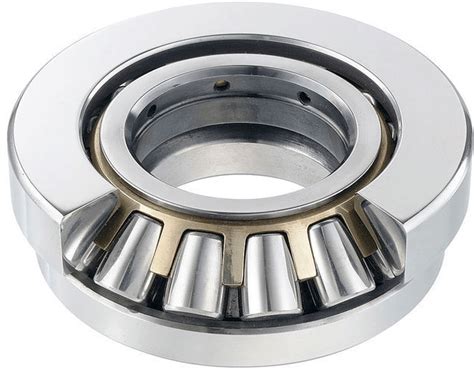
-
Ball thrust bearings offer low friction and high-speed capabilities, making them ideal for applications in precision machinery and power tools.
-
Roller thrust bearings boast higher load capacities than ball thrust bearings and are commonly used in heavy-duty machinery, gearboxes, and turbines.
-
Tapered roller thrust bearings combine the strength of tapered rollers with the load-bearing capacity of thrust bearings, making them suitable for applications involving extreme loads and misalignment.
The Benefits of Deploying Thrust Bearings
Integrating thrust bearings into your systems offers a multitude of advantages that can enhance performance, reduce maintenance costs, and extend equipment lifespan. Here are some compelling reasons to consider using thrust bearings:
-
Exceptional Load Capacity: Thrust bearings excel in handling axial loads, allowing equipment to operate under demanding conditions without compromising stability or reliability.
-
Reduced Friction and Energy Loss: Thrust bearings are designed to minimize friction, resulting in lower energy consumption and improved overall efficiency.
-
Extended Equipment Life: By preventing excessive wear and tear on critical components, thrust bearings contribute to extended equipment life and reduced maintenance downtime.
-
Reliable Operation in Harsh Environments: Thrust bearings are often constructed from durable materials and are equipped with advanced seals to ensure reliable operation in demanding environments, including extreme temperatures, dust, and contamination.
Case Studies: Thrust Bearings in Action
The practical applications of thrust bearings extend to a wide range of industries, including:

-
Wind turbines: Thrust bearings support the massive rotor assemblies of wind turbines, enabling them to generate clean energy efficiently.
-
Electric motors: Thrust bearings ensure smooth and reliable operation of electric motors in various industrial applications, from machine tools to electric vehicles.
-
Gearboxes: Thrust bearings play a crucial role in managing axial loads in gearboxes, reducing noise and vibration and extending the life of gears.
Humorous Stories and Lessons Learned
Throughout the history of thrust bearings, there have been many humorous anecdotes that illustrate their importance and the lessons we can learn.

- One story recounts an incident where a mechanic mistakenly installed a radial bearing instead of a thrust bearing in a high-speed gearbox. The result was catastrophic, as the gearbox quickly failed due to excessive axial loads. The lesson learned here is the importance of using the correct type of bearing for each application.
- Another tale involves a team of engineers who spent countless hours troubleshooting a noisy turbine gearbox. Eventually, they discovered that the thrust bearings were not properly lubricated, causing excessive wear and vibration. This incident highlights the crucial role of proper lubrication in maintaining bearing performance.
- In a humorous twist, one engineer was tasked with designing a thrust bearing for a new product. After numerous failed attempts, he finally realized that he had been using the wrong calculation formula. The lesson learned from this experience is the importance of double-checking calculations and relying on credible resources.
Crucial Factors to Consider When Selecting Thrust Bearings
To ensure optimal performance and longevity of thrust bearings, careful consideration should be given to the following factors:
-
Load Capacity: Determine the maximum axial load that the bearing will be subjected to during operation.
-
Speed: Consider the rotational speed of the bearing and select a bearing that can handle the required speed without generating excessive friction or vibration.
-
Lubrication: Choose a bearing that is compatible with the available lubrication system and that can operate reliably in the specific operating environment.
-
Environmental Conditions: Assess the operating environment and select a bearing that is designed to withstand any extreme temperatures, dust, or contamination that may be present.
Guidance for Implementing Thrust Bearings in Your Systems
To achieve maximum benefits from thrust bearings, follow these guidelines:
-
Proper Installation: Ensure proper installation of the thrust bearing in accordance with manufacturer's specifications to prevent premature failure.
-
Regular Maintenance: Implement a regular maintenance schedule to monitor bearing performance, lubricate as needed, and replace bearings when necessary.
-
Expert Consultation: Consult with a bearing specialist or manufacturer to discuss specific application requirements and receive expert advice on bearing selection and maintenance.
The Future of Thrust Bearings: Innovation and Advancements
The world of thrust bearings is constantly evolving, with ongoing research and development leading to innovative designs and materials. Here are some emerging trends:
-
Advanced Materials: New materials, such as ceramic composites and graphene-enhanced polymers, are being explored for thrust bearings to enhance load capacity and reduce friction.
-
Integrated Sensors: Thrust bearings are being integrated with sensors to monitor bearing performance and provide real-time data for predictive maintenance.
-
Active Control Systems: Active control systems are being developed to adjust thrust bearing alignment and loads dynamically, optimizing performance and extending bearing life.
Conclusion: Empower Your Systems with Thrust Bearings
Thrust bearings are indispensable components in the world of rotary motion. Their ability to manage axial loads with precision and reliability has revolutionized industries and paved the way for advancements in energy, transportation, and manufacturing. By understanding the benefits, types, and applications of thrust bearings, you can harness their power to enhance the performance, efficiency, and longevity of your systems.
Empower your systems with thrust bearings today and unlock the full potential of rotary motion.
Call to Action
Contact our team of experts to discuss your specific thrust bearing requirements. We can assist you in selecting the ideal bearing for your application, ensuring optimal performance and extended equipment life.
Helpful Resources
Tables
Feature |
Description |
Load Capacity |
The maximum axial load that the bearing can support without failure. |
Speed |
The maximum rotational speed that the bearing can handle without excessive friction or vibration. |
Lubrication |
The type of lubrication required for the bearing to operate reliably. |
Type of Thrust Bearing |
Applications |
Ball Thrust Bearings |
Precision machinery, power tools |
Roller Thrust Bearings |
Heavy-duty machinery, gearboxes, turbines |
Tapered Roller Thrust Bearings |
Extreme loads, misalignment |
Industry |
Applications |
Wind Turbines |
Rotor assemblies |
Electric Motors |
Smooth operation, reduced noise |
Gearboxes |
Managing axial loads, extending gear life |