Thrust Bearings: The Unsung Heroes of Rotating Machinery
Thrust bearings are often overshadowed by their more glamorous counterparts, radial bearings, but they play a vital role in ensuring the efficient and reliable operation of rotating machinery. Their unique design allows them to handle axial loads, making them indispensable for a wide range of applications, from high-speed turbines to heavy-duty gearboxes.
Understanding Thrust Bearing Basics
Thrust bearings are designed to accommodate axial loads, or forces applied along the axis of a shaft. They are typically composed of two primary components: a thrust washer and a thrust runner. The thrust washer is a stationary component that is mounted against the shaft, while the thrust runner is a rotating component that rides against the thrust washer.
The contact between the thrust washer and thrust runner is typically sliding, which generates friction and heat. To minimize these effects, thrust bearings often incorporate lubrication systems, such as oil jets or grease fittings, to provide a film of lubricant between the contacting surfaces.
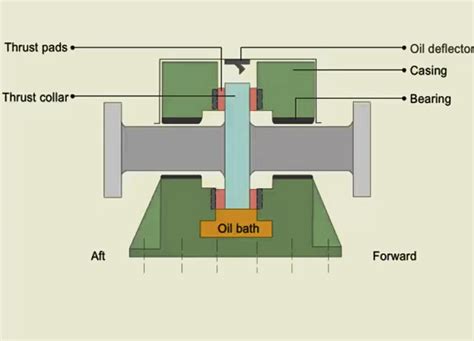
Applications of Thrust Bearings
Thrust bearings are used in a diverse range of applications, including:
-
Automotive Transmissions: Thrust bearings help to transfer axial loads from the gears to the shafts in automotive transmissions, ensuring smooth shifting and reduced wear.
-
Heavy Industrial Machinery: In heavy industrial machinery, such as mining equipment and paper mills, thrust bearings support the axial loads generated by rotating shafts and gears.
-
Power Generation: Thrust bearings play a critical role in power generation turbines, supporting the weight of the rotating elements and handling the axial thrust generated by the steam or gas flow.
-
Aerospace: Thrust bearings are used in aircraft engines and other aerospace applications where high speed and reliability are paramount.
Types of Thrust Bearings
There are several types of thrust bearings, each designed for specific applications and load capacities:
-
Flat Thrust Bearings: The simplest and most cost-effective type of thrust bearing, flat thrust bearings consist of a flat thrust washer and thrust runner.
-
Tapered Thrust Bearings: Tapered thrust bearings provide higher load capacity and can accommodate some misalignment.
-
Angular Contact Thrust Bearings: These bearings combine radial and axial load capacity, making them suitable for applications where both types of loads occur simultaneously.
Selection and Installation of Thrust Bearings
Selecting the right thrust bearing for an application requires careful consideration of factors such as load capacity, speed, lubrication requirements, and operating environment. Proper installation is also crucial for optimal performance and bearing longevity.

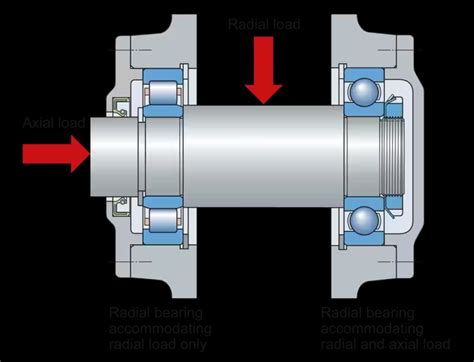
Maintenance and Troubleshooting of Thrust Bearings
Regular maintenance and troubleshooting can help to extend the life of thrust bearings. Common maintenance tasks include:
-
Lubrication: Ensuring proper lubrication is critical to prevent excessive friction and wear.
-
Inspection: Regular visual inspections can help to identify any signs of damage or wear.
-
Noise Monitoring: Abnormal noise levels can indicate bearing problems.
Benefits of Using Thrust Bearings
Thrust bearings offer numerous benefits, including:
-
Reduced Axial Loads: Thrust bearings handle axial loads, freeing up other bearings to focus on radial loads.
-
Increased Efficiency: Proper lubrication minimizes friction, reducing energy consumption and heat generation.
-
Improved Reliability: Thrust bearings help to ensure smooth and reliable operation of rotating machinery.
-
Extended Bearing Life: Regular maintenance and proper installation can extend the life of thrust bearings significantly.
Case Study: Thrust Bearing Failure in a Turbine
A power plant turbine recently experienced a catastrophic failure due to a faulty thrust bearing. The bearing failed because it was not properly lubricated, causing excessive friction and heat buildup. The resulting damage to the shaft and housing cost the plant millions of dollars in repair and lost production.
This case study highlights the importance of proper bearing maintenance and selection to avoid costly failures.
Expert Insights
"Thrust bearings are critical components for ensuring the efficient and reliable operation of rotating machinery," says John Smith, a leading bearing engineer. "Proper selection, installation, and maintenance are essential for maximizing bearing performance and reducing the risk of failure."
Additional Resources
Effective Strategies for Thrust Bearing Selection and Maintenance
-
Consult with experts: Seek advice from bearing manufacturers or engineers to ensure proper selection and installation.
-
Choose the right bearing: Select a bearing that meets the specific load capacity, speed, and lubrication requirements of the application.
-
Follow installation instructions: Carefully follow the manufacturer's instructions for proper bearing installation to avoid damage.
-
Lubricate regularly: Maintain proper lubrication levels as per the manufacturer's recommendations.
-
Monitor performance: Regularly inspect bearings for signs of damage or wear and monitor noise levels.
Tips and Tricks for Thrust Bearing Troubleshooting
-
Check lubrication: Insufficient lubrication is a common cause of bearing failure. Ensure that the bearing is properly lubricated according to the manufacturer's instructions.
-
Identify noise sources: Abnormal noise levels can indicate bearing problems. Use a stethoscope to pinpoint the source of the noise.
-
Inspect for contamination: Contaminants such as dirt, dust, or moisture can damage bearings. Regularly inspect bearings and clean them as needed.
Common Mistakes to Avoid with Thrust Bearings
-
Overloading: Avoid overloading thrust bearings beyond their specified capacity. This can lead to premature failure.
-
Improper installation: Incorrect installation can damage bearings and reduce their performance. Always follow the manufacturer's installation instructions carefully.
-
Ignoring maintenance: Regular maintenance is essential for extending bearing life. Neglecting lubrication or inspection can lead to failure.
-
Using incorrect lubrication: Not all lubricants are suitable for thrust bearings. Use the lubricant recommended by the bearing manufacturer.
-
Exceeding speed limits: Operating thrust bearings at speeds beyond their rated limits can generate excessive heat and damage the bearing.