Replacing Bearings: A Comprehensive Guide to Extending Equipment Life
Bearings play a pivotal role in the smooth operation of machinery across various industries. However, with time and usage, bearings inevitably experience wear and tear, leading to potential equipment failures and costly downtime. Replacing bearings proactively can prevent these issues, ensuring optimal performance and maximizing equipment lifespan.
Table 1: Frequency of Bearing Replacement
Industry |
Average Replacement Interval |
Automotive |
50,000 - 100,000 miles |
Industrial Machinery |
3 - 5 years |
Power Generation |
10 - 15 years |
Table 2: Signs of Bearing Failure
Symptom |
Cause |
Excessive Noise |
Worn-out bearings |
Increased Vibration |
Misaligned bearings |
Overheating |
Lubrication failure |
Case Study: Benefits and How-to
Scenario: A manufacturing plant experienced frequent bearing failures in its conveyor system, resulting in costly downtime.

Benefit: By replacing the bearings with high-quality, heavy-duty bearings, the plant significantly reduced downtime and increased production efficiency.
How-to:
-
Identify the faulty bearings: Determine the bearings causing the failures through vibration analysis or other diagnostic methods.
-
Choose the right bearings: Select bearings designed for the specific application and load requirements, considering factors such as speed, temperature, and lubrication.
-
Proper installation: Ensure bearings are correctly installed and aligned to avoid premature wear.
Case Study: Advanced Features and Challenges
Scenario: A wind turbine operator sought to upgrade the bearings in its turbines with advanced features to improve reliability and performance.
Advanced Features:
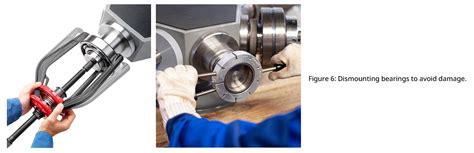
-
Condition monitoring: Sensors integrated into the bearings allowed for real-time monitoring of temperature, vibration, and other parameters.
-
Self-lubrication: Bearings designed with self-lubricating materials reduced maintenance requirements and extended lifespan.
Challenges:
-
Cost: Advanced bearings typically come with a higher upfront investment.
-
Compatibility: Ensuring compatibility with existing systems can require modifications or redesigns.
Effective Strategies for Replacing Bearings
-
Regular Maintenance: Implement a proactive maintenance schedule that includes regular lubrication, inspection, and monitoring.
-
Early Detection: Utilize diagnostic tools to identify early signs of bearing failure, enabling timely replacement.
-
Correct Installation: Train technicians on proper bearing installation techniques to prevent premature failure.
-
High-Quality Bearings: Invest in bearings from reputable manufacturers that meet or exceed industry standards.
-
Consider Advanced Features: Explore advanced bearing technologies that offer condition monitoring, self-lubrication, and other benefits.
-
Seek Professional Advice: Consult with bearing experts or engineers to ensure optimal bearing selection and replacement strategies.
Common Mistakes to Avoid
-
Ignoring Warning Signs: Neglecting signs of bearing failure can lead to catastrophic equipment breakdown.
-
Using Incorrect Bearings: Selecting bearings that are not suitable for the application can result in premature failure.
-
Improper Installation: Improper installation or alignment can cause early bearing wear and vibration.
-
Infrequent Maintenance: Lack of regular maintenance leads to bearing deterioration and reduced equipment lifespan.
-
Neglecting Lubrication: Inadequate or improper lubrication is a major contributor to bearing failure.
Pros and Cons of Replacing Bearings
Pros:
-
Extended Equipment Life: Replacing bearings proactively reduces the risk of catastrophic failures and extends equipment lifespan.
-
Reduced Downtime: Timely bearing replacement minimizes unplanned downtime and improves production efficiency.
-
Improved Performance: New bearings ensure optimal equipment performance and prevent performance degradation.
-
Cost Savings: Regular bearing replacement can prevent costly equipment repairs and downtime.
Cons:
-
Initial Investment: Replacing bearings involves an upfront investment in parts and labor.
-
Downtime During Replacement: Equipment must be taken offline for bearing replacement, resulting in potential downtime.
-
Potential Compatibility Issues: Ensuring compatibility with existing systems can require modifications or redesigns.
Making the Right Choice
Choosing the right bearing replacement strategy depends on specific application requirements and constraints. By considering the pros and cons, mitigating risks, and seeking professional advice, businesses can make informed decisions that optimize equipment performance and longevity.
Conclusion
Replacing bearings is a crucial aspect of equipment maintenance that can significantly extend equipment life, prevent downtime, and improve performance. By understanding the signs of bearing failure, implementing effective replacement strategies, and avoiding common mistakes, businesses can reap the benefits of optimal bearing performance and maximize the return on their equipment investment.