Which Was the First Industrial Robot?
The first industrial robot was the Unimate, developed by George Devol and Joseph Engelberger and installed in a General Motors factory in New Jersey in 1961. The Unimate was a programmable, computer-controlled mechanical arm that could perform repetitive tasks such as welding, painting, and assembly.
Since then, industrial robots have become an essential part of manufacturing, with an estimated 2.7 million units in operation worldwide in 2020, according to the International Federation of Robotics. Industrial robots are used in a wide variety of industries, including automotive, electronics, food and beverage, and pharmaceuticals.
There are many benefits to using industrial robots, including:
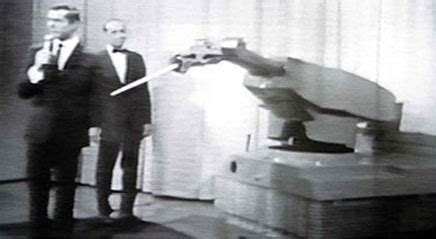
- Increased productivity
- Improved quality
- Reduced costs
- Increased safety
- Greater flexibility
Industrial robots can be programmed to perform a wide variety of tasks, from simple repetitive tasks to complex assembly operations. They can be used to weld, paint, assemble, inspect, and package products. Industrial robots can also be used to perform hazardous tasks, such as working with chemicals or in high-heat environments.
The use of industrial robots is expected to continue to grow in the coming years. As robots become more sophisticated and affordable, they will be increasingly used to perform a wider range of tasks in a variety of industries.
Year |
Number of Industrial Robots in Operation Worldwide |
2015 |
1.5 million |
2020 |
2.7 million |
2025 (projected) |
4 million |
Industry |
Number of Industrial Robots in Operation |
Automotive |
1.2 million |
Electronics |
500,000 |
Food and beverage |
200,000 |
Pharmaceuticals |
100,000 |
Success Stories
-
Ford Motor Company uses industrial robots to weld car bodies. The company has installed more than 1,000 robots in its assembly plants, which has helped to increase productivity and reduce costs.
-
Apple Inc. uses industrial robots to assemble iPhones. The company has installed more than 10,000 robots in its factories, which has helped to improve quality and reduce costs.
-
Amazon.com uses industrial robots to pick and pack orders in its warehouses. The company has installed more than 100,000 robots in its warehouses, which has helped to increase productivity and reduce costs.
Effective Strategies, Tips and Tricks
-
Choose the right robot for the job. There are many different types of industrial robots available, so it is important to choose the right one for the specific task.
-
Program the robot correctly. Industrial robots must be programmed correctly in order to operate safely and efficiently.
-
Train operators properly. Operators must be properly trained in order to operate industrial robots safely and effectively.
-
Maintain the robot regularly. Industrial robots must be maintained regularly in order to keep them operating at peak performance.
Common Mistakes to Avoid
-
Not choosing the right robot for the job. Choosing the wrong robot for the job can lead to decreased productivity, increased costs, and safety hazards.
-
Not programming the robot correctly. Incorrectly programming the robot can lead to safety hazards, decreased productivity, and increased costs.
-
Not training operators properly. Improperly trained operators can pose a safety hazard to themselves and others, and they may not be able to operate the robot efficiently.
-
Not maintaining the robot regularly. Failure to maintain the robot regularly can lead to decreased performance, increased costs, and safety hazards.
Getting Started with Which Was the First Industrial Robot**

-
Identify the need for a robot. Determine what tasks need to be automated and what the benefits of automation would be.
-
Research different types of robots. There are many different types of industrial robots available, so it is important to research the different options and choose the right one for the specific task.
-
Get a quote from a robot supplier. Once you have chosen a robot, get a quote from a supplier. The quote should include the cost of the robot, installation, training, and maintenance.
-
Install the robot. Once you have purchased the robot, it will need to be installed. The installation process should be performed by a qualified technician.
-
Train operators. Once the robot is installed, operators will need to be trained on how to operate the robot safely and efficiently.
-
Maintain the robot. The robot will need to be maintained regularly in order to keep it operating at peak performance.
Why Which Was the First Industrial Robot Matters
Which was the first industrial robot is important because it has revolutionized the manufacturing industry. Industrial robots have helped to increase productivity, improve quality, reduce costs, increase safety, and increase flexibility. As robots become more sophisticated and affordable, they will be increasingly used to perform a wider range of tasks in a variety of industries.
Here are some of the key benefits of using which was the first industrial robot:
-
Increased productivity: Industrial robots can work faster and more consistently than humans, which can lead to increased productivity.
-
Improved quality: Industrial robots can perform tasks with greater precision and accuracy than humans, which can lead to improved quality.
-
Reduced costs: Industrial robots can be used to automate tasks that are currently performed by humans, which can lead to reduced costs.
-
Increased safety: Industrial robots can be used to perform hazardous tasks, such as working with chemicals or in high-heat environments, which can lead to increased safety.
-
Greater flexibility: Industrial robots can be reprogrammed to perform different tasks, which can lead to greater flexibility.
Challenges and Limitations
Which was the first industrial robot also has some challenges and limitations.

-
Cost: Industrial robots can be expensive to purchase and maintain.
-
Complexity: Industrial robots can be complex to program and operate.
-
Safety: Industrial robots can pose a safety hazard if they are not properly operated and maintained.
-
Job displacement: Industrial robots can displace human workers, which can lead to job losses.
Potential Drawbacks
-
High initial investment: The initial investment in an industrial robot can be high.
-
Complexity of programming: Programming an industrial robot can be complex and time-consuming.
-
Need for skilled labor: Skilled labor is required to operate and maintain industrial robots.
-
Safety concerns: Industrial robots can pose a safety hazard if they are not properly operated and maintained.
Mitigating Risks
-
Conduct a thorough cost-benefit analysis. Before purchasing an industrial robot, it is important to conduct a thorough cost-benefit analysis to determine if the investment is justified.
-
Invest in training. Operators must be properly trained in order to operate industrial robots safely and effectively.
-
Implement proper safety measures. Proper safety measures must be implemented to prevent accidents involving industrial robots.
-
Redeploy displaced workers. Workers who are displaced by industrial robots can be redeployed to other jobs within the company.
Industry Insights
The which was the first industrial robot industry is expected to continue to grow in the coming years. As robots become more sophisticated and affordable, they will be increasingly used to perform a wider range of tasks in a variety of industries.
Here are some of the key industry insights:
-
Growing demand for industrial robots: The demand for industrial robots is expected to grow in the coming years. This growth is being driven by the increasing need for automation, the rising cost of labor, and the growing popularity of e-commerce.
-
New applications for industrial robots: Industrial robots are being used in a wider range of applications, including manufacturing, healthcare, and logistics.
-
Advancements in technology: Industrial robots are becoming more sophisticated and affordable. This is making them more accessible to a wider range of businesses.
Maximizing Efficiency
There are a number of things that can be done to maximize the efficiency of which was the first industrial robot.
-
Choose the right robot for the job. The first step to maximizing efficiency is to choose the right robot for the job. There are many different types of industrial robots available, so it is important to choose the one that is best suited for the specific task.
-
Program the robot correctly. The robot must be programmed correctly in order to operate safely and efficiently.
-
Train operators properly. Operators must be properly trained in order to operate the robot safely and efficiently.
-
Maintain the robot regularly. The robot must be maintained regularly in order to keep it operating at peak performance.
-
Use the robot in a clean and safe environment. The robot should be used in a clean and safe environment to prevent damage and extend its lifespan.
FAQs About Which Was the First Industrial Robot**
What is the which was the first industrial robot?
Which was the first industrial robot is a programmable, computer-controlled mechanical arm that can perform repetitive tasks such as welding, painting, and assembly.
What are the benefits of using which was the first industrial robot?
There are many benefits to using which was the first industrial robot, including increased productivity, improved quality, reduced costs, increased safety, and greater flexibility.
What are the challenges and limitations of using which was the first industrial robot?
Which was the first industrial robot also has some challenges and limitations, including cost, complexity, safety, and job displacement.